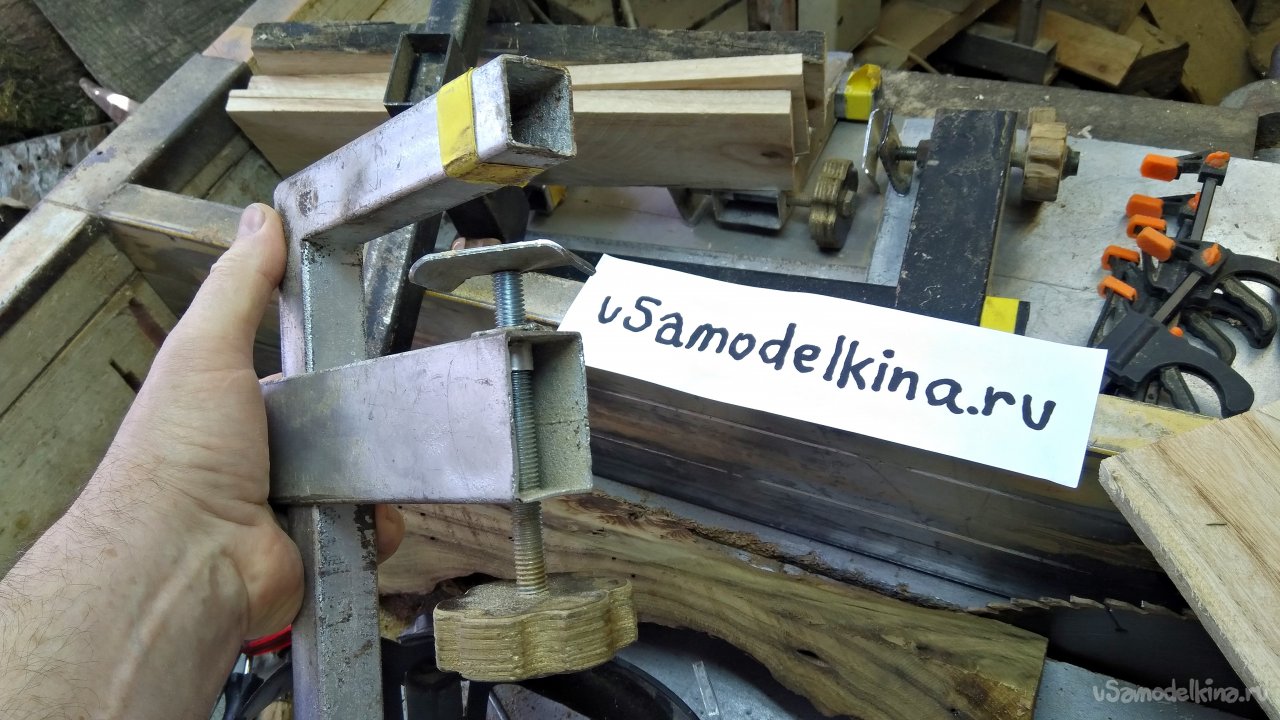
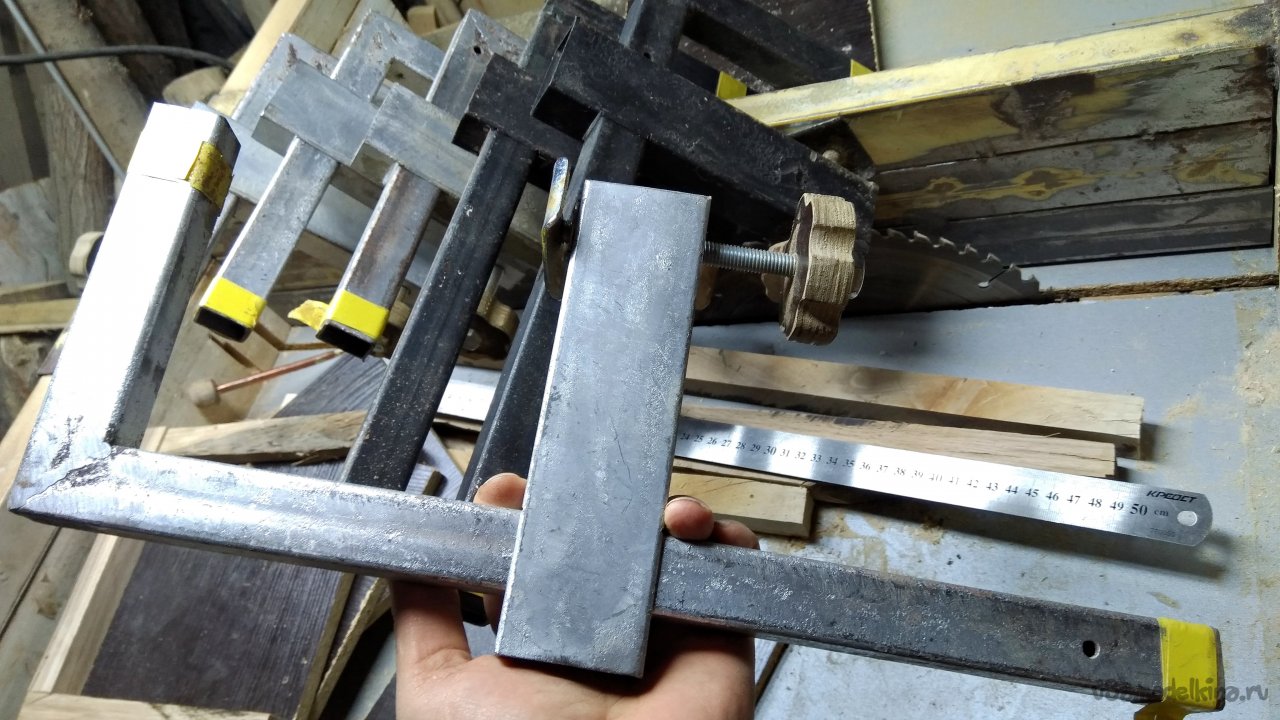
Понадобились мне струбцины для столярных работ. То что у меня есть, меня не устраивают, мала сила прижима, пластиковые хлипкие детальки, ими зажать вообще нормально нельзя, даже палец себе не прищемить )) Ну в общем решил я делать самостоятельно. Посмотрел, конечно, по ценам и качеству, то что меня условно может устроить, начинается ценник с двух тысяч за штуку, это плохонькие которые ещё и неудобные. Минимум их надо шесть, а лучше десять.
А вот которые прямо ух! Хочу! Стоят немыслимых денег, вот например Bessey GH40, примерно 15 тысяч рублей за штуку. Но я пока не готов на такие траты.
Железячки у меня разные есть. Чего не нашёл, купил а автомагазине и в хозяйственном.
Болты, гайки, электроды, отрезные камни на болгарку, краску аэрозольную, изоленту. Профильные трубы у меня были.
Приступил к изготовлению. Прорезал болгаркой отверстия равные сечению тонких профильных труб. Они должны с минимальным зазором входить и перемещаться в своих местах. Просверлил отверстия для мебельных закладных гаек, у меня М10, по болтам подбирал, болты даже не знаю от чего, но катаные и крепкие. Что-то ими в автомобильном моторе крепилось. Но думаю любые подходящие можно использовать. Все досужие измышления что на струбцинах должна быть особая упорная резьба, это просто маркетинговый ход. На мебельных забивных гайках отломал острые усики, которые предназначены для вбивания в дерево, у меня они ведь приварены будут.
Болты доработал, обточил на них начало резьбы до диаметра отверстия в упорных пятаках. Упорные пятаки тоже не помню откуда у меня, но такие можно сделать, просто отковав углубление в железной пластине в пару миллиметров толщиной.
Надев упорный пятак на утоньшение на болте, расклепал кончик этого утоньшения, пятак упорный прокручивается, но не выпадает.
Приварил гайку к профильной трубе, и сварив угол 90 градусов при помощи магнитного угольника, который сам накануне сделал из неисправного жёсткого диска компьютера. Дело в том, что там стоят очень мощные магниты, я подумал, чего пропадать добру, когда мне нужен для сварки магнитный угольник. Я пользовался фабричными, но или неправильно их сделали, или магниты слабые были, мне не понравились. А тут почто всё готово, разобрал жёсткий диск, вырезал в его дюралевом корпусе на боковых стенках отверстия по размеру магнитов, и закрепил их туда.
Для того чтоб свариваемые детали сами держались под правильным углом, магниты разместил ниже привалочной плоскости на 0,1 миллиметра. Магниты сильные, держат крепко.
После сварки окрасил из аэрозольного баллончика детали, и после сушки собрав струбцины, намотал кусочки изоленты на концы струбцины, с одной стороны, чтобы не выскочила упорная часть с Г-образной части, а на упорной части для того, чтобы не заминалось дерево при зажиме.
Года два я уже активно ими пользуюсь, силу прижима не измерял, но считаю достаточной, без подкладок зажимаю не очень ответственные детали, вмятин не остаётся. На пробу зажимал сосновую вагонку 100 миллиметров шириной, трещит и выгибается доска, а струбцинам нипочём. Я попрыгал на этой досочке, явно мне её не сломать, а струбциной можно ))
Инструменты что я использовал:
Болгарка, сварочный аппарат, магнитный угольник.
Ну и при работе обязательно очки, рукавицы сварочные, очки и защитная сварочная маска.
Материалы:
Профильные трубы. 25 х 28 мм и 30 х50 мм
Профильные трубы некоторые от списанного автобуса "Икарус", они покрыты бесшумкой типа каучука, поэтому вид корявый, ну и "родные" фирменные цвета кое-где проглядывают ))
Г-образная часть 150 мм, «хвостик» по желанию, у меня порядка 400 мм.
Зависит от того насколько большие вам нужны струбцины.
Размеры произвольные, я использовал самый «ленивый» вариант, когда одна профильная труба вставляется в другую, но можно использовать одинакового сечения, тогда придётся наварить накладки для создания окна в котором будет двигаться подвижная часть струбцины.
Болты и гайки М10. Болты примерно 100 мм.
Длинные не нужны, так-как губки сдвигаются свободно, болтом только дотягивание осуществляется.
Расходники;
Краска, изолента, электроды, отрезные камни на болгарку.
Набор железок для изготовления струбцины. Есть у меня заводские, но они меня не устраивают, сила прижима мала, крутить долго под размер, решил сделать чтобы быстро менялся размер.
Тиски я уже сделал быстрозажимные для сверлильного станка. Вот сейчас зажимаю в них кленовый обрезок, чтобы сделать барашек, которым будет крутиться винт.
Сверлить сверлом 10 миллиметров сразу не стал, сначала пилотные отверстия, так поточнее получается.
Потом рассверливаю отверстия по внешнему краю
Сначала сверлю отверстия по внешнему краю, потом балеринкой вырезаю по этим отверстиям, образуется типа накатки крупной ))
Болт М10 вкручиваю в деревяшку с натягом. Идет со скрипом, но мне и нужна тугая посадка.
Для того, чтобы упор, которым будет прижиматься деталь не вращалась вместе с болтом, на болте делаю проточку и одеваю на него пластинку с выштамповкой которая позволит скрыть выступающий конец болта. Чтобы не повредить зажимаемую деталь.
Расклёпываю выступающую часть болта, но оставляю слабину для того, чтоб пластина не крутилась вместе с болтом.
Отверстия прорезал болгаркой, и потом тонким зубилом прорубал углы.
Подготовил все детали для сварки, закладная гайка для мебельных работ удлинённая, вот она и будет служить в паре с болтом на затяжку.
Для сварки, чтобы не держать детали, из неисправного винчестера сделал магнитный угольник 90 градусов.
Вытащил из него магниты, там весьма мощные они, и закрепил на боковой поверхности прорезав предварительно под них гнёзда. Магниты на 0,1 мм ниже плоскости боковой, усилия удержания вполне хватает.
Вот, например этим магнитным угольником из HDD несу сварочный аппарат, даже за угол хватает силы у магнита удержать его.
Для сварки всё готово, единственное неудобство заметил при сварке, если дуга близко к магниту, она искривляется и нормально не заварить.
На видео первая струбцина уже готова, показываю как она работает, ну и набор для изготовления второй струбцины тоже тут.
Проверка силы прижима. Попробовал обычную вагонку 100 мм зажать, проложил бруски чтобы видно было как будет деформироваться.
Ну в общем усилие килограммов двести с гаком, я с весом 90 кг становился на эту досочку, она чуть прогнулась, струбциной до треска легко, далее я не стал давить, никто так сжимать не будет их, вмятины остаются на дереве.
Первая пара готова. Но мне понравилось, струбцин много не бывает, буду делать ещё! ))
Далее по накатанной, подготовка железяк. Решил сразу сделать несколько, конструкция проста, делается легко.
Сделал шаблон из тонкой дощечки, для разметки барашков. Чтоб не рисовать каждую заготовку заново.
Сначала сделал несколько из первой попавшейся деревяшки, но при закручивании болтов расколол эту деревяшку повдоль, поэтому решил барашки делать из фанеры.
Их сломать не получится, такая фанера весьма крепка.
После сварки решил их сразу окрасить. Красил правда без соблюдения правил, не грунтовал, да и в один слой. Лишь бы ржавчину укрыть ))
Никакой особой красоты от них не требуется, серебрянкой из баллончика легко и просто окрашивается.
Готовые изделия. Жёлтая изолента не для красоты. С одной стороны, не даёт соскользнуть подвижной лапке, а на самой лапке для того, чтобы минимизировать вмятины на дереве, которое зажимаю.
310 миллиметров ширина раскрыва, но струбцины легко масштабируются, хоть три метра можно сделать из такой профильной трубы.
Года два назад их делал, думаю это самый простой и надёжный вариант струбцин, и почти даром ))
За два года краска пооблупилась, да и красил я по ржавому и без грунтовки, но они и не для красоты делались, мне вот прямо сейчас надо было ))
Гайка мебельная удлиненная, но можно и простые использовать, М10 вполне достаточно крепости для работы с деревом.
Ну и наконец скомпилированный файл со всеми фотками и видео.
На ютубе Ссылка на видео есть пара десятков видео с моими поделками. Если кому интересно, могу описать что и как делал.
Становитесь автором сайта, публикуйте собственные статьи, описания самоделок с оплатой за текст. Подробнее здесь.