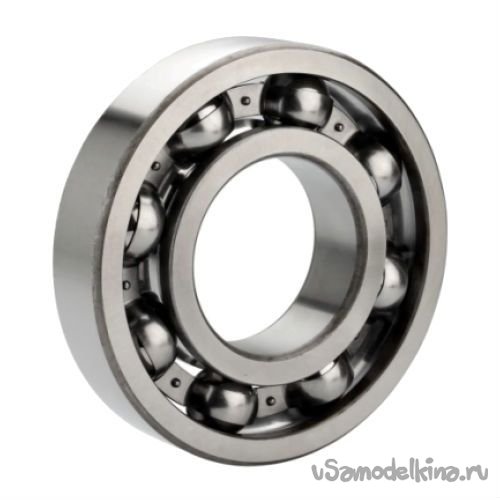
Эта сталь применялась в СССР для производства шариков и обойм подшипников среднего размера. Для малых размеров применялась ШХ-9 с меньшим содержанием хрома. Для очень крупных подшипников применялась цементируемая сталь более сложного состава. Специальные стали применялись для кислотостойких или жароустойчивых подшипников. «15» и «9» означают содержание хрома в десятых долях процента, а углерода в этих сталях около одного процента. Этому же составу соответствует инструментальная сталь «Х», но она более низкого качества по однородности. Таким образом, ШХ-15, это сталь высокого качества, твёрдая и принимающая закалку в масле (или даже в горячей воде) из-за наличия хрома, который замедляет распад аустенита в перлитные и бейнитные структуры. Высокое содержание углерода обеспечивает высокую твёрдость, а хром, кроме улучшения условий закалки, измельчает зерно, делая эту сталь более вязкой, по сравнению со сталью тех же напильников.
Чтобы сделать эту сталь «нержавеющей», полтора процента хрома совершенно недостаточно, так как пороговая концентрация хрома для высокой коррозионной стойкости составляет больше двенадцати процентов. ШХ-15 коррозирует в воде, как обычные стали, и даже сильнее, из-за большого количества углерода. Наличие большого количества углерода, кроме увеличения твёрдости, способствует сохранению при закалке мягкого аустенита вплоть до комнатных температур, что иногда нежелательно. Остаточный аустенит может быть разрушен охлаждением изделия после закалки на несколько часов до минус двадцати градусов или даже обычным отпуском. Но в ШХ-15 остаточного аустенита не много и он на твёрдость сильно не влияет.
Эта сталь весьма универсальна. Высокая твёрдость и мелкое зерно позволяет применять её вместо «Быстрореза» для токарных резцов и работать с малым углом заточки. Конечно, скорость резания приходится снижать в несколько раз, но часто это не слишком накладно, так как резцы специального назначения применяются не часто. Длинные отрезные, расточные или фигурные резцы, особенно, для обработки алюминия или пластиков, имеет полный смысл напаивать ШХ-15. Тем более, что эта сталь, в отличие от Быстрореза, отлично паяется латунью с бурой, а её термическая обработка не идёт ни в какое сравнение по сложности с той же Р-18. Охладив резец после напайки, его рабочую часть нужно повторно нагреть до температуры закалки и закалить в масле, после чего подогреть до появления бледно-жёлтого цвета побежалости. Понятно, что можно закаливать только режущую часть резца. Контролировать твёрдость можно просто напильником. Закалённую сталь он совершенно не берёт.
Ковка этой стали возможна при относительно невысокой температуре, от восьмисот до шестисот градусов.
Добыча стали из старых подшипников имеет свои особенности. Разбивать подшипники молотком опасно, можно лишиться глаз или получить серьёзные ранения острыми осколками. Поэтому обойма шарикоподшипника разрезается «Болгаркой», после чего её можно разогнуть, нагревая её среднюю часть любой подходящей горелкой до свечения и разгибая вручную, клещами или плоскогубцами. Постепенно кольцо распрямляется и идёт на ковку под молоток даже четыреста грамм. Для кузнечной обработки небольших деталей, вроде зубил, стамесок, кухонных и сапожных ножей вполне достаточна горелка с электролизёром и гремучим газом мощностью два с половиной киловатта, а уж кислорода с пропаном хватит и подавно! Горелку можно применять и для местной закалки крупных и общей закалки местных деталей.
Температуру нагрева можно контролировать визуально, по цвету свечения, однако в руководстве по эксплуатации этой стали, (например Гуляев, «Металловедение») рекомендуется узкий диапазон температур нагрева под закалку, а именно 830-840 градусов Цельсия. Поэтому предпочтительнее электропечь с термопарой и равномерным нагревом рабочего пространства. Калибровать термопару для этого диапазона можно по температуре плавления чистого алюминия (660 градусов) или хлористого натрия (801 градус). С другой стороны, в книге Гуляева, в разделе о поверхностной закалке, есть весьма интересные указания на то, что при быстром нагреве структурные изменения в металле полностью успевают произойти только при более высокой температуре, чем при медленном печном нагреве. Поэтому, при нагреве под закалку высокотемпературным пламенем или ТВЧ, с одной стороны, надо повышать температуру нагрева, а с другой, это не должно вызвать нежелательный рост зерна. То есть, быстро нагревая будущее лезвие инструмента горелкой, нужно греть до большей температуры, потом подстудить слегка металл, обдувая его воздухом несколько секунд и погрузить в масло.
Тут есть несколько тонкостей. Изделия, типа ножей или топоров, с тонким лезвием, в закалочной ванне сначала остынут в своей тонкой части, которая будет сжиматься быстрее, чем толстое сечение и может потрескаться. (Эта проблема как раз частично решается наличием в стали хрома и возможностью её закалки в масле, а не в воде.) Поэтому кухонные или сапожные ножи, лезвия топоров нужно погружать в закалочную ванну в последнюю очередь, начиная погружения с толстых сечений изделия, (обухом вниз!). Ножи проще закалить в виде исходной пластинки равной толщины, погружая в закалочную ванну вертикально и после этого уже аккуратно заточить, не перегревая на заточке тонкое лезвие.
Обязательно для любой «обычной» стали нужно после закалки провести отпуск. Отпуск стали снимает закалочные напряжения, делает её более мягкой, но, в то же время, и менее хрупкой. При отпуске в интервале 250-400 градусов, согласно тому же Гуляеву, все стали охрупчиваются, что называется «отпускная хрупкость первого рода». У многих легированных сталей есть ещё и «отпускная хрупкость второго рода», но стали с «особыми» видами термообработки мы здесь не рассматриваем. Насколько охрупчивание при отпуске вредно именно для ШХ-15, можно проверить, отковав узкую полоску стали, правильно закалив её и после отпуска при разной температуре по длине, посмотреть хрупкость, ломая в тисках.
Для деталей шарикоподшипников из этой стали рекомендуется отпуск при 150-160 градусов в течении одного-двух часов, а для прецизионных подшипников, которые не должны менять свои размеры при эксплуатации, рекомендуется сразу после закалки, до отпуска, обработка холодом при минус двадцати, чтобы разложить остаточный аустенит.
На Металлическом форуме вопрос об отпуске тоже поднимался.
« 23.12.2018 в 03:43, Valekvoi сказал:
спустя сутки сделал отпуск
уже неправильно, чем быстрее - тем лучше, желательно не более, чем через 15 минут!
Если хотите нож из ШХ сделать твердый и максимально нехрупкий - с отпуском придется повозиться не по-детски: калить в горячее (130-140С) масло, вынув из масла моментально (не давая остыть) - в духовку на 130С на 15 часов, охладить до комнатной и снова в духовку на 150С на 1,5 часа.»
Комментирую: Предложенная технология отпуска напоминает один из вариантов термообработки «Быстрореза» и высокоуглеродистой инструментальной стали Х12, при котором остаточный аустенит разлагается длительным и многократным отпуском. Духовка представляется излишней, так как можно просто держать металл в масляной ванне при нужной температуре нужное время.
Эксплуатационные свойства изделий из ШХ-15 высокие! Для стамески, лезвие которой было заточено под угол градусов на двадцать и просто отпущено нагревом от толстой части до соломенного цвета, срубание не очень толстых гвоздей в дереве не приносит особого вреда. Зубило, отпущенное до синего цвета нагревом от нерабочей части, хрупковатое, но работает неплохо! Резец фигурный по алюминию сделал с одной заточкой сто деталей и следов износа не имеет. К кухонному ножу женщины сумели подобрать «ключи». Они режут варёное мясо в глубоком блюдце, при этом лезвие скрежещет по фарфору, а в таком режиме работы даже «Победит» затупится быстро, но, в целом, нож острее обычного заводского ножа из советской углеродистой нержавейки! К сожалению, нож чернеет и требует протирки насухо после работы, чего с нержавейкой, разумеется, не происходит. Ножик типа скальпеля, но побольше, позволяет использовать его, как шабер, снимать фаски на алюминии и железе, срезать заусеницы и после этого худо-бедно точить карандаши.
Подводя итог, следует заметить, что для инструментов, рассчитанных на удары или изгибы (зубила, ножи, особенно, охотничьи, которые работают на морозе и должны быть «сверхнадёжными»), следовало бы применить более легированную сталь, которую без потери твёрдости можно было бы отпускать при температуре 400-450 градусов. Это снизило бы и «отпускную хрупкость» и остаточные напряжения. Такие стали описаны в уже упомянутой книге Гуляева, которая заслуживает всяческих похвал и за простоту и понятность изложения и за широкий охват тем и за глубоко научный подход к проблемам термообработки.
Бондаренко, Маяки, 2019 года.