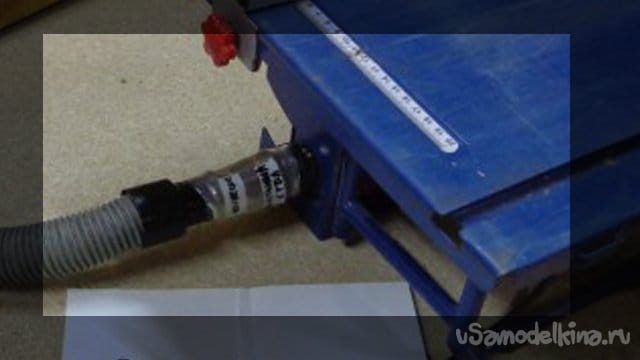
Приветствую всех самодельщиков!
В данной статье хочу поделиться опытом ещё одного стружкоотвода, но уже для станка по распилу досок вдоль. Очень удобный при распиле на рейки или как ещё говорят «ламели».
Я его называю просто «Пильный столик».
В статье «Стружкоотвод на пылесос для электрорубанка из РЕТ бутылок» делал для рубанка, и идея себя показала с положительной стороны.
Поначалу просто вставлял шланг в «родной» стружкоотвод станка, он сделан так, чтобы шланг надевался на него, но у меня такого шланга нет.
Когда делал «Большой бак для пылесоса Makita 440, НЕ ЦИКЛОН», шланг взял от старого бытового пылесоса, а у них у всех трубки на конце шланга практически одинакового диаметра.
Так что буду отталкиваться от того что есть!
Инструменты и материалы:
- бутылочки РЕТ объёмом 0,33
- канцелярский нож
- строительный фен (термопистолет)
- кусок провода
- ватные палочки
- белая изолента для надписей
Вот такой станочек у меня и очень удобный, глубина пропила 45 мм и столешница поворачивается под углом 45 градусов.
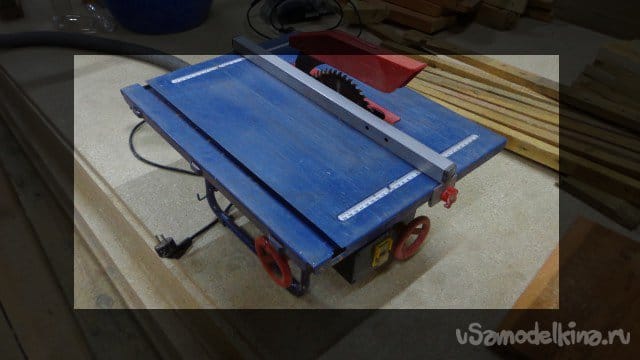
Причина придумывания такого стружкоотвода, такая же как и в "Стружкоотвод на пылесос для электрорубанка из РЕТ бутылок", при пилении ДСП, ДВП, фанеры, ламината и обычных досок, пыли было очень много, и чтобы не утруждать себя уборкой "пылевых барханов" после работы, решил повторить идею.
Купил пять бутылочек с соком, объёмом 0,33 литра. Опустошил их и промыл их водой.
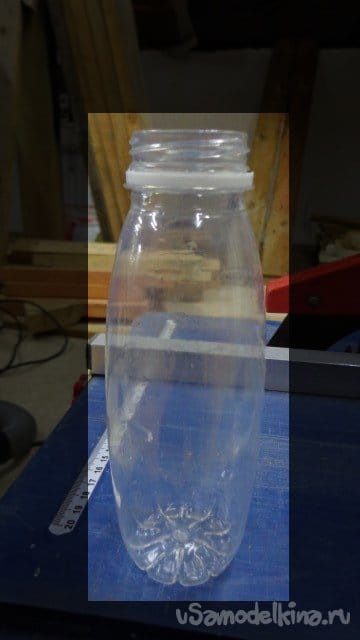
Шланг на пылесосе по внутреннему диаметру практически такой же как и внутренний диаметр стружкоотвода на станке. Пылесос подключается проблематично, а во время работы шланг постоянно задевается и выскакивает.
Если постоянно впихивать трубку шланга в стружкоотвод станка, то со временем на нём может появиться трещина, так как трубка шланга будет давить изнутри, а при постоянных задеваниях шланга тем более будет нагрузка, которая и спровоцирует трещину.
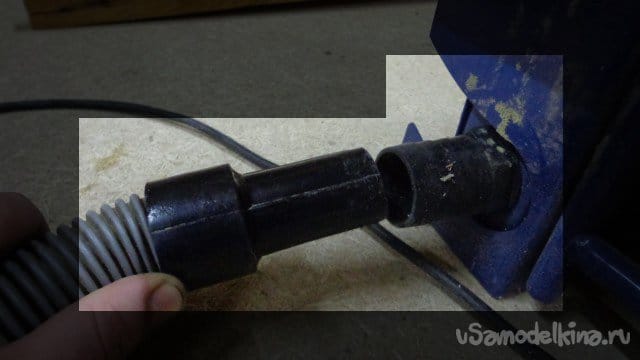
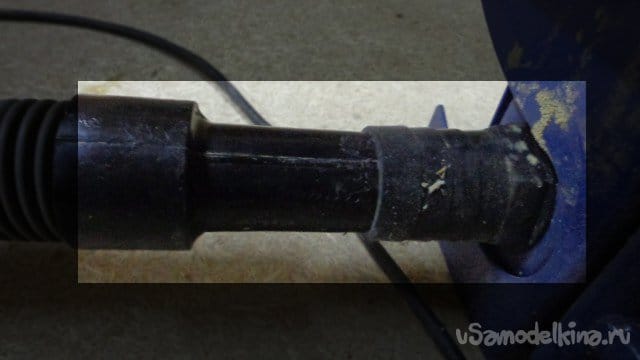
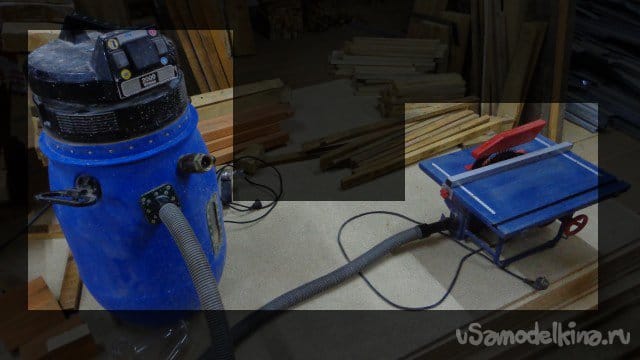
В чём плюс иметь такой пылесос, он синхронизирован с электроинструментом (можно подключать через пылесос электроинструмент мощностью до двух киловатт), включаешь станок и сразу включается пылесос, опилки и пыль что осталась внутри станка также втягивается в пылесос, после выключения станка, пылесос работает ещё около пяти секунд (вытягивает пыль из шланга) и сам отключается.
Бутылочки нарезал на глаз, так как при обработке строительным феном, пластик РЕТ сжимается как в диаметре так и по длине, и если отрезать 12 см, то после обработки горячим воздухом, трубка может стать длинной около 8 см (приблизительно). (на следующих фото видно)
От дна отступил около 1 см, а от горлышка в месте где бутылочка начала заужаться.
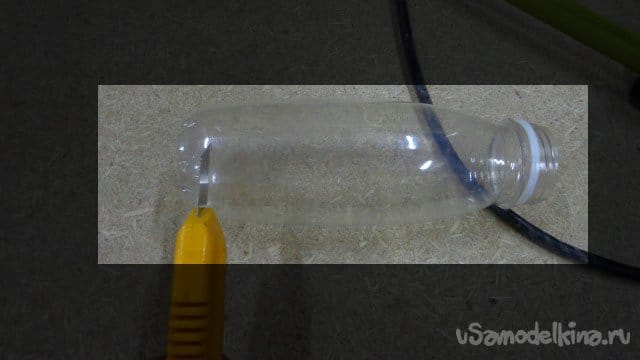
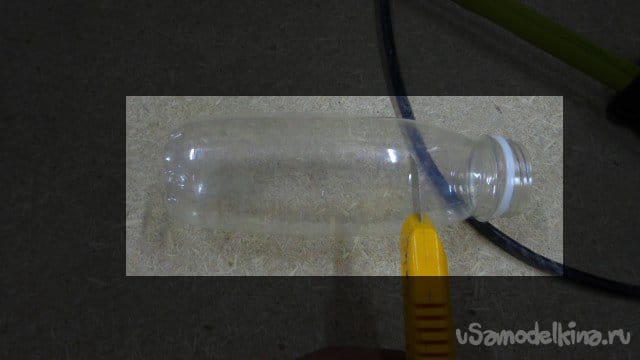
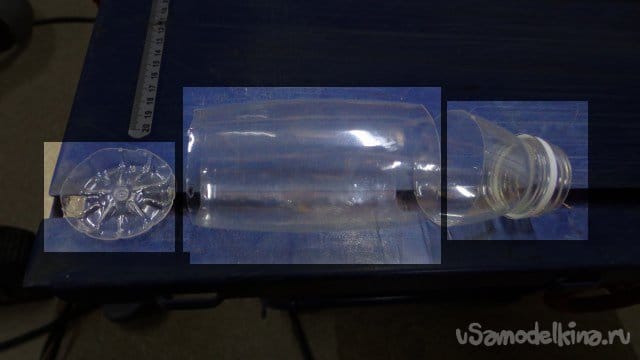
От и До... (было /стало)
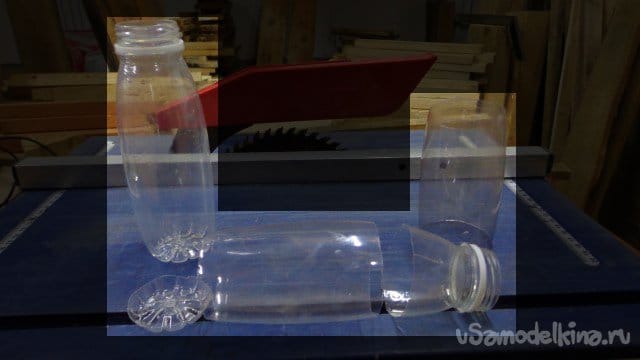
Вот такая получилась трубочка, "термоусадочная".
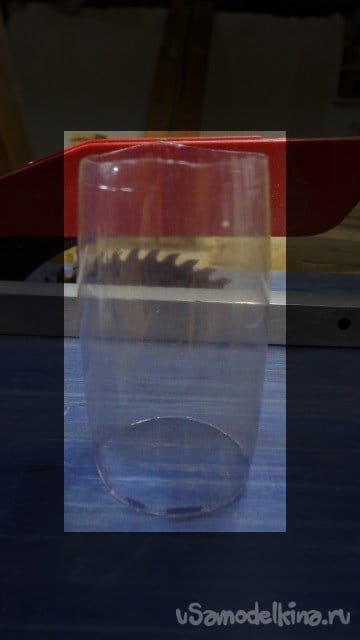
Поставил станок на бок и хотел было уже приступить, но...
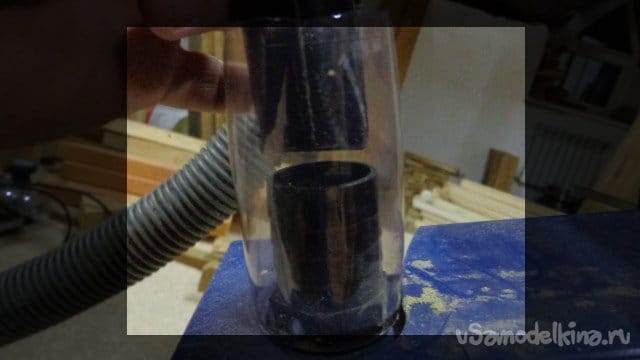
...забыл про проволоку, с помощью её сделать ребро жёсткости.
На самом стружкоотводе станка имеется рифлёная поверхность и можно было бы не делать ребро.
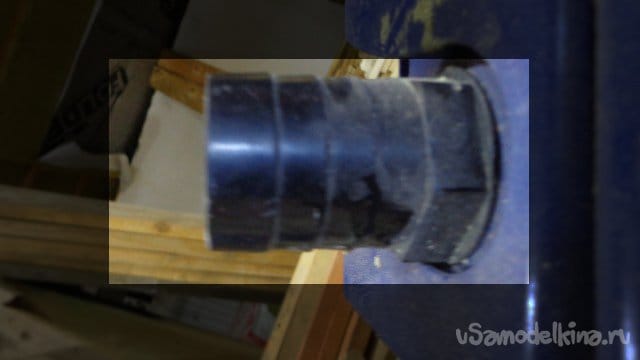
Но на всякий случай решил сделать, так как рифлёность маленькая, да и мне при необходимости нужно снимать самодельный стружкоотвод.
Взял медную проволоку в сечении 2,5 кв.мм и накрутил их на трубки шланга и стружкоотвода станка.
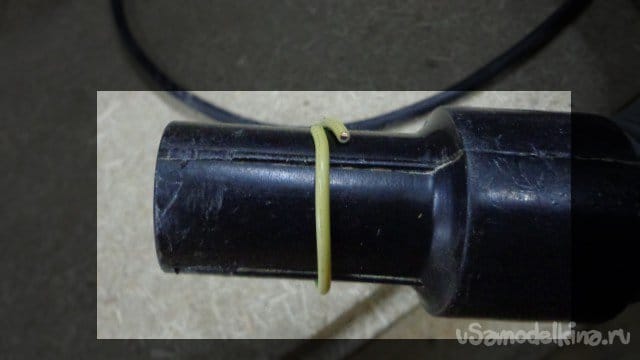
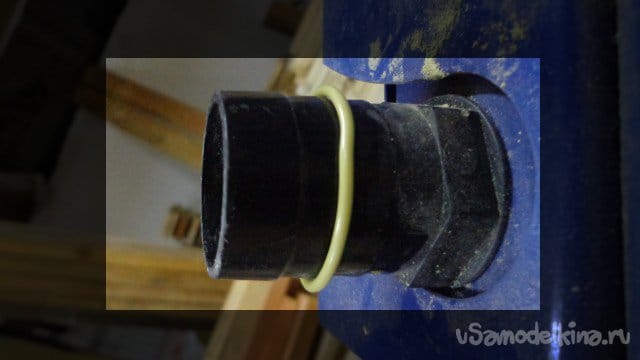
Вот теперь можно обрабатывать трубку горячим воздухом.
Надел на стружкоотвод станка и вставил шланг от пылесоса.
Начал обрабатывать горячим воздухом, пока не сядет плотно, надо же чтобы шланг не выскакивал!
Обрабатывал температурой 400°C, так как бутылочки используемые при данной самоделке более плотные, и при меньшей оптимальной температуре усаживаются медленно, а мне надо было побыстрее выполнить данную идею и продолжить работу с пилением всего деревосодержащего материала.
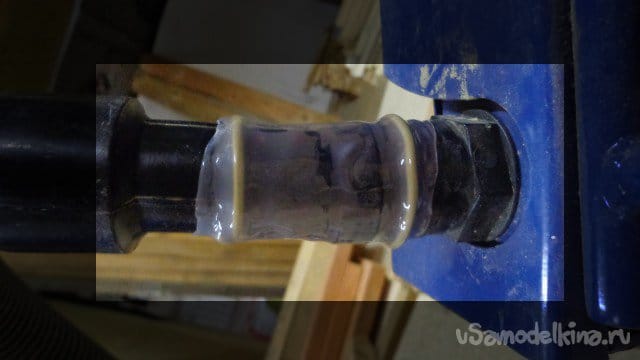
Совет!!!
При обрабатывании РЕТа горячим воздухом, советую феном водить из стороны в сторону плавно и не держать его на одном месте, тогда РЕТ "усадится" равномерно. (на фото выше видны грубые края).
Перед работой с этой идеей снимал с рубанка готовый стружкоотвод и обнаружил что начал "хрустеть", не знаю сколько он "проживёт", но решил для станка стружкоотвод усилить...
Из-за постоянных задеваний шланга может расслоится и начать деформироваться внутри, и в итоге может выскочить первая трубка или последняя, информация не точная, но лучше предусмотреть возможную проблему.
Усиливать буду палочками от ватных палочек.
Усиление будет придавать не палочки, а форма РЕТа по верх данных палочек.
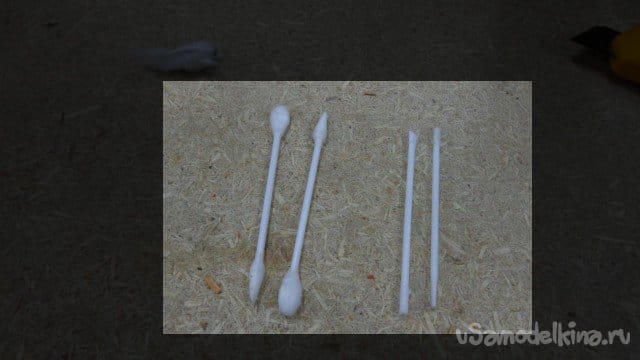
Отрезал канцелярским ножом концы с ватками и подрезал чтобы эти палочки находились между кольцами из проволоки.
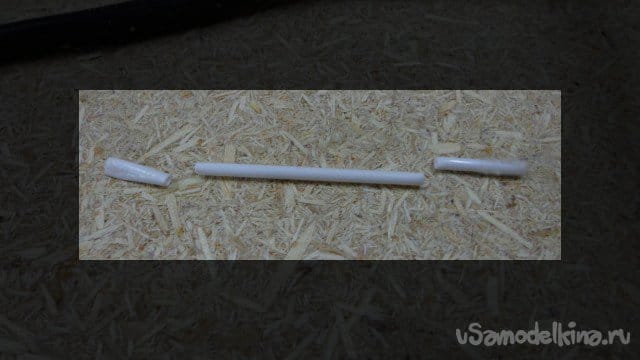
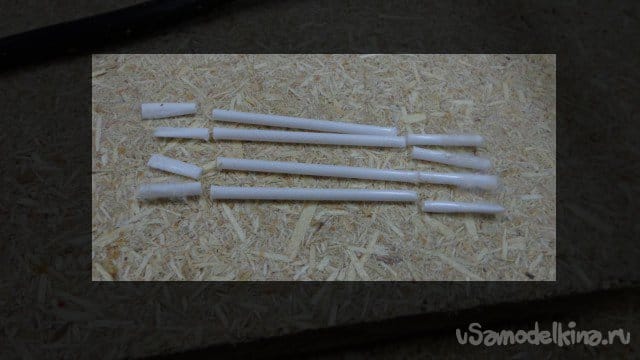
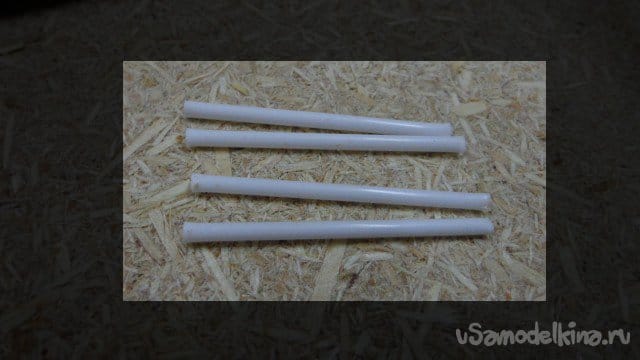
Зафиксировал палочки белой изолентой.
Отрезал от мотка полосу и потом разрезал на две полоски меньшей шириной.
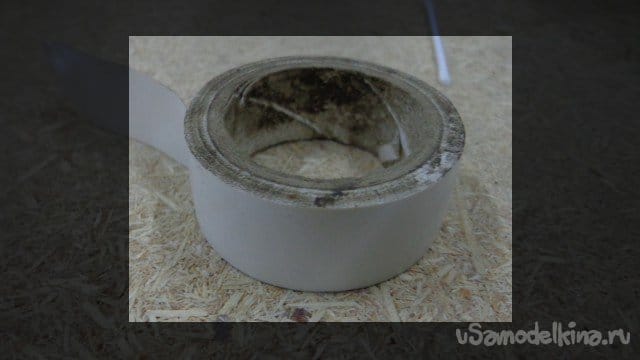
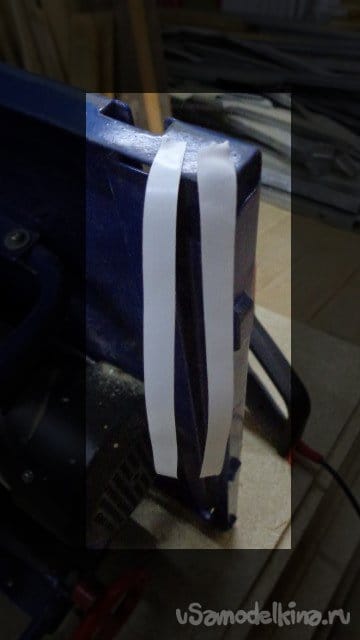
После примотал палочки. Изолента останется внутри, так как она никак не помешает.
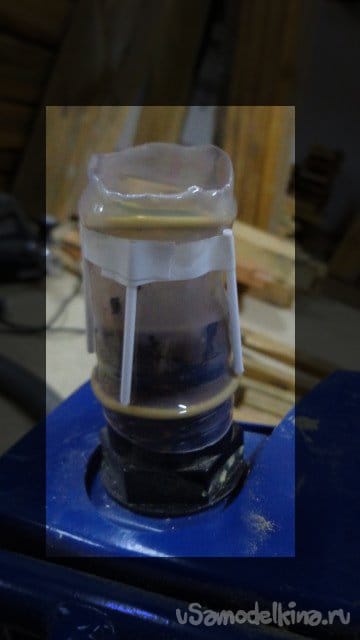
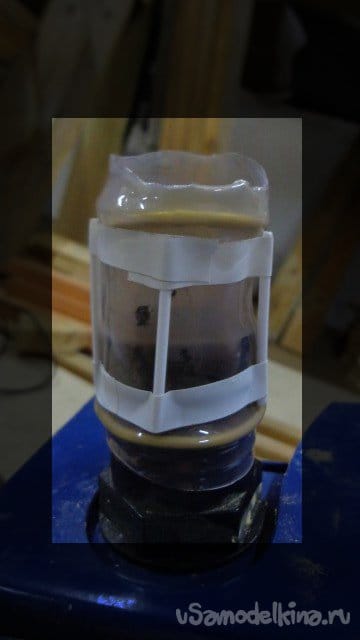
После надел следующую трубочку и обработал горячим воздухом.
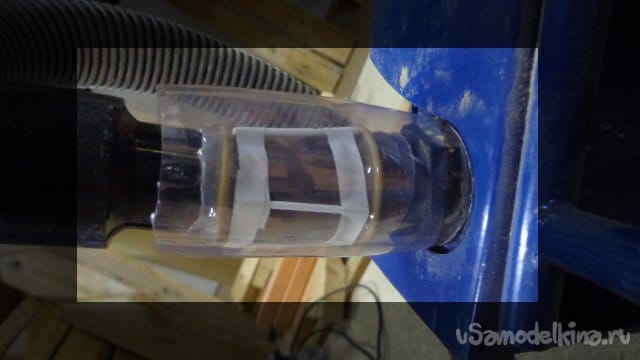
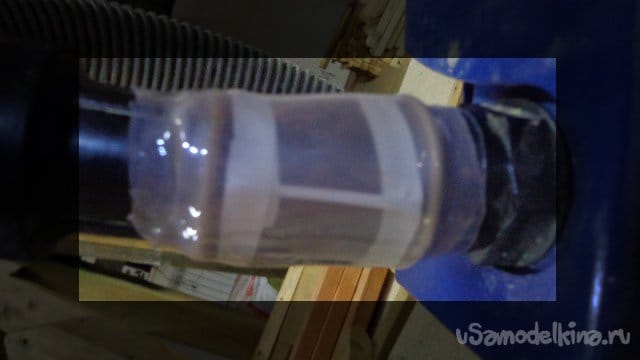
Как четвёртая трубочка была обработана феном, решил сделать надписи на концах стружкоотвода.
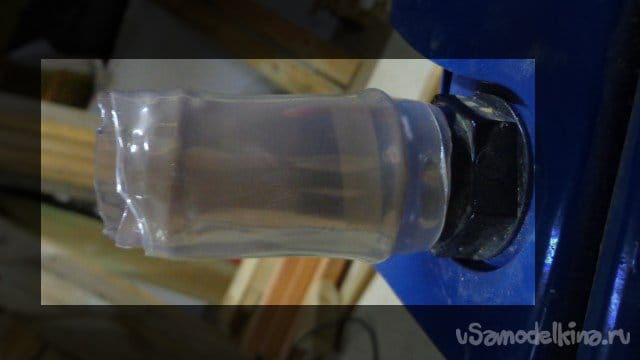
Малоли для чего потребуется снять самодельный адаптер на стружкоотвод, а как надевать обратно, так придётся потратить время, так как у шланга и стружкоотвода станка внешние диаметры практически одинаковые, а надевается и снимается этот адаптер тяжело (это хорошо)...
Написал маркером прямо на мотке белой изоленты "пильный стол" и "пылесос".
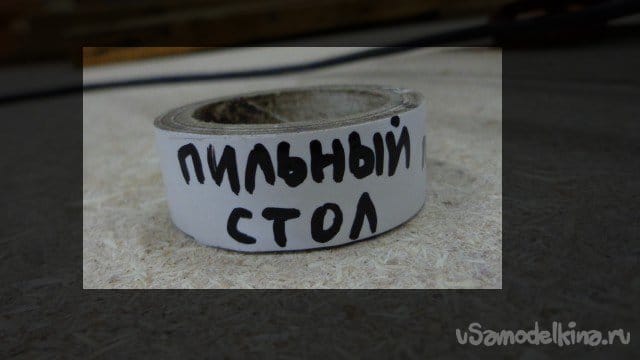
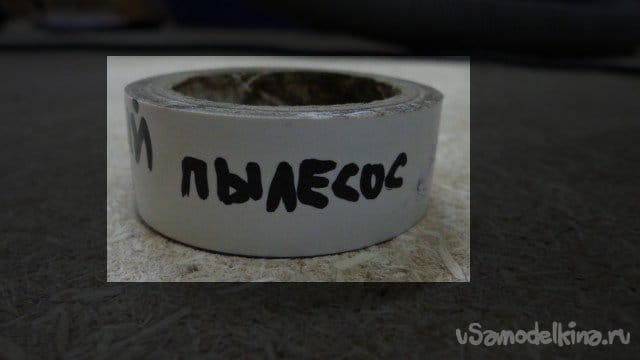
Отрезал канцелярским ножом и наклеил на адаптер.
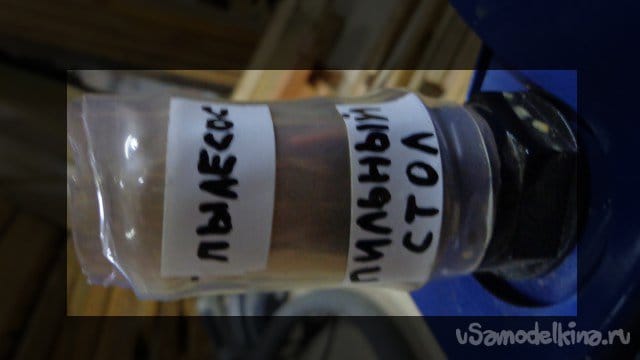
Теперь можно надевать последнюю трубку и обрабатывать горячим воздухом.
Вот тут из-за моей спешки испортилась надпись, маркер не успел высохнуть и буквы смазались, РЕТ-трубка при усаживании сдвинулась и стёрла надпись, главное что остальное осталось :)
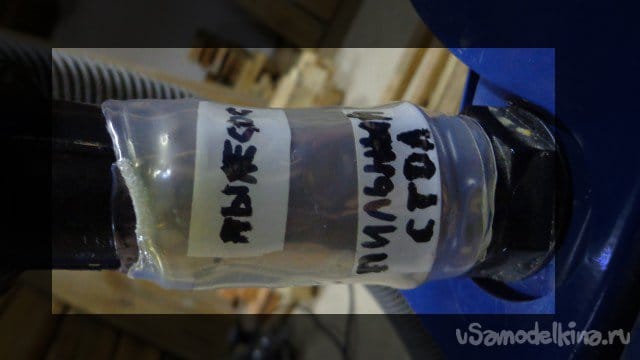
После остывания пластика снял (с трудом со станка) и подрезал неровный край и вытащил проволоку изнутри поддев её шилом.
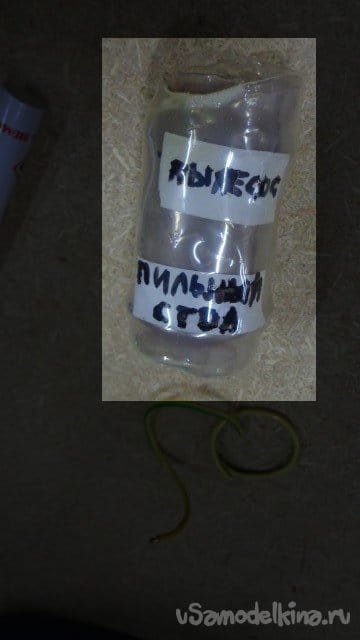
Даже когда станок стоит в стороне надетый адаптер на стружкоотводе не мешается.
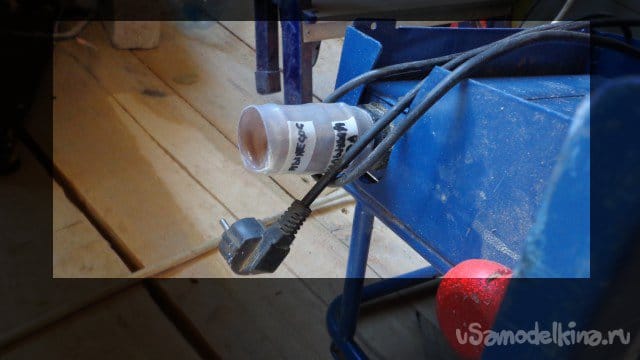
Теперь можно спокойно работать и дышать полной грудью не используя респиратор при пилении деревосодержащего материала.
Фото снято в процессе работы, пыль конечно некуда не делась, но на много чище стало и респиратором не пользуюсь.
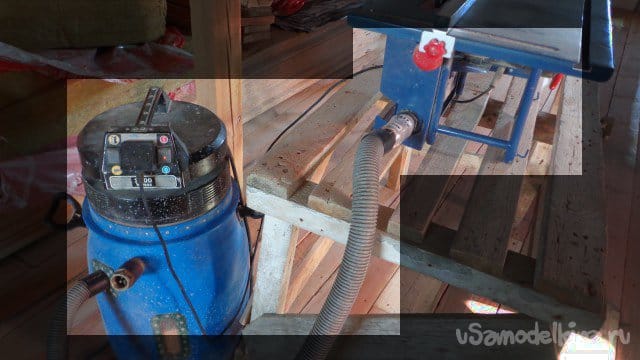
Такой адаптер можно сделать для любого электроинструмента.
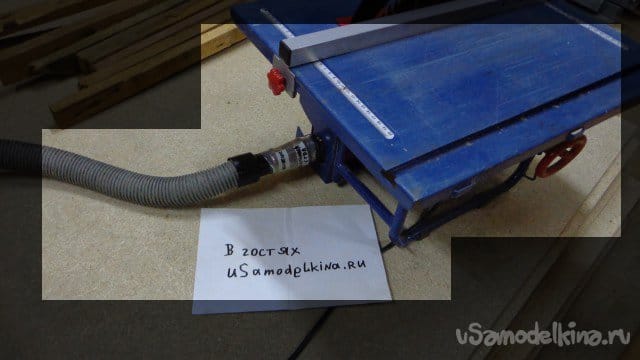
Всем успехов и спасибо что прочитали статью...