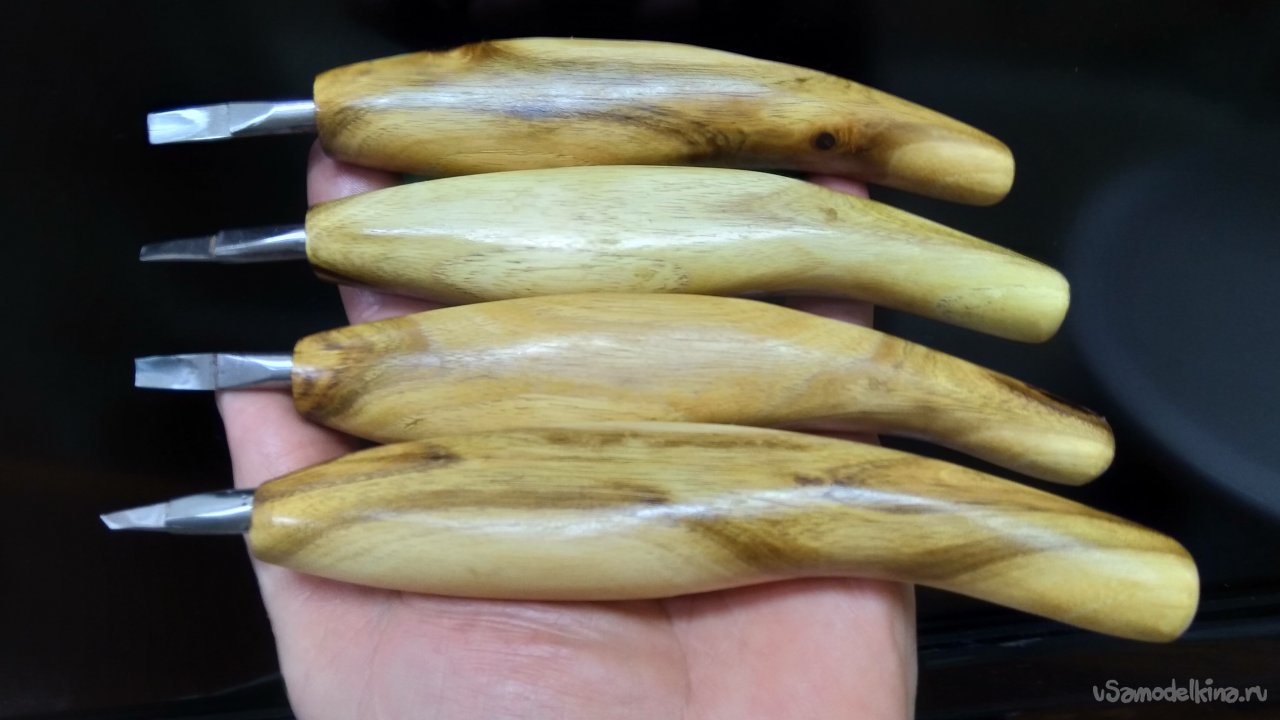
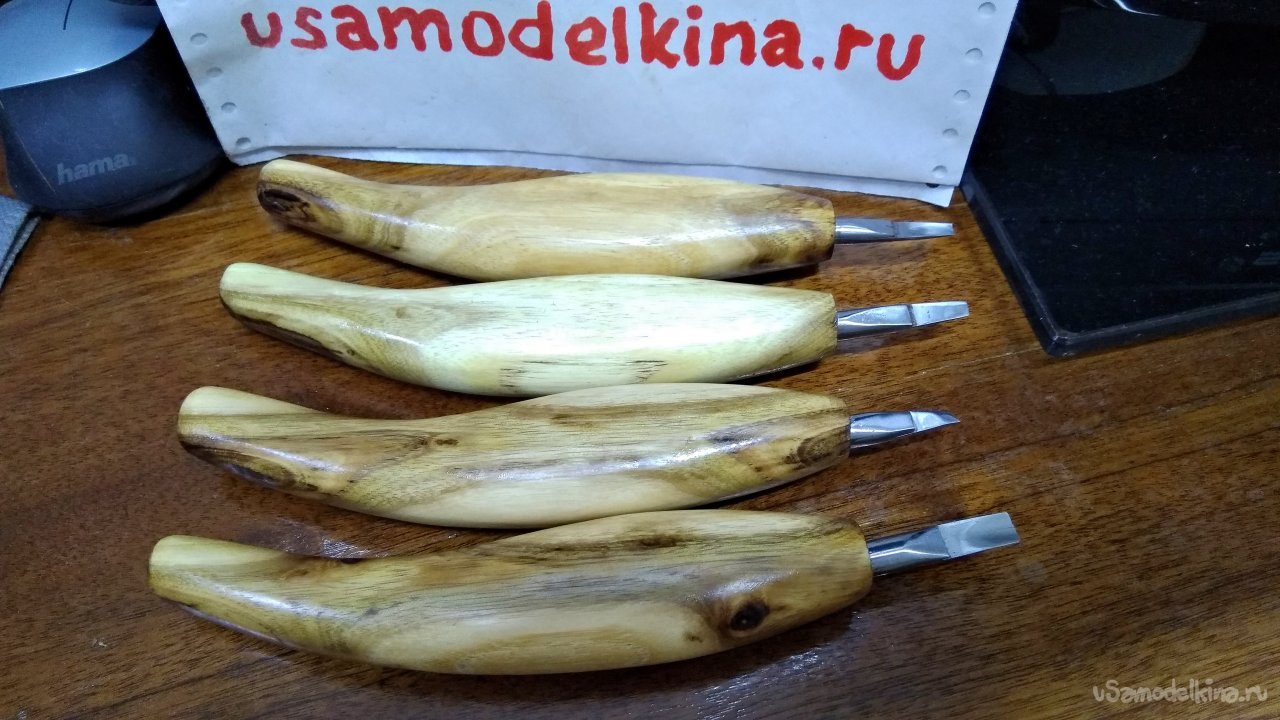
Комплект ножей, о которых я уже рассказывал, зарекомендовал себя хорошо. Удобные рукоятки, достаточная острота лезвий, но они для очень твёрдых пород дерева тяжелы. Просто трудно воткнуть в дуб или граб поперёк волокон. А я как раз затеял ремонт солонки, она у меня из дуба сделана. Но ножи в дуб лезут очень туго, ширина лезвия тех ножей что я сделал ранее, для мягких пород дерева годится вполне, яблоня, орех грецкий, орех пекан, камфорный лавр, слива и алыча режутся легко, а вот дуб уже трудно, поэтому задумал сделать комплект ножей меньшего размера. Рукоятки напилил из веток чёрной акации. Это одно из самых твёрдых пород древесины. Примерно вдвое твёрже берёзы, и немного твёрже дуба. Для клинков решил использовать листовую пружину от старой стиральной машинки, они там служили для успокоения биения стирального барабана. Сталь, вроде подходящая по крепости. Конструкцию держателя стального вставыша в мягкий пруток я и раньше использовал. Так и качественная сталь экономится, и надёжность повышается. Закрепить тонкое стальное лезвие в рукоятке несколько проблематично, а если это же лезвие врезать в пруток большого диаметра, то проблем вообще нет. Сверлится отверстие в рукоятке и туда вставляется этот пруток с уже приваренным электросваркой заточенным лезвием. Пропил делал болгаркой, тонкие диски как раз образуют нужную ширину пропила. Но его можно и поджать немного, для плотной посадки. Приваривал вставыш только в самой глубине пропила, щёчки пропила спереди образуют некоторое подобие пружины которые смягчают боковые усилия на лезвие. Варил электросваркой зажав клинок в медный теплоотвод. К сожалению, один желобчатый нож треснул повдоль, или когда я его отковал, или пережал при сварке зажимая через теплоотвод в тисках. А может и то и другое. Но я не опечалился, даже если отломается часть, такой узенький нож тоже сгодится.
Ещё одна неприятность пришла откуда не ждал, аварийно завершила работу ленточная шлифовальная машинка, с брызгами расплавленного металла. Думал всё, совсем сгорела. Но решил проверить что там у неё внутри. Щётки изношены и не видно на них характерного блеска, значит они уже не прижимались к коллектору с нужной силой. Таких щёток дома не оказалось, купил в ближайшем автомагазине. Взял пару комплектов, не часто их меняю, да и есть запас других. Попытался спрессовать съёмником дюралевый шкив приводной с мотора. Но похоже конструкторы не задумывались о ремонтопригодности, материал дюрали хрупкий, при попытке снять, обломились щёчки шкива на нижнем ручье сразу с двух сторон, как раз под лапками съёмника. Точить такой шкив у меня желания нет, решил собрать без шлифовки ламелей якоря. Сквозь отверстия для щёток, вид был удовлетворительный. Установил щётки, включил без ремня, и мотор заработал как ни в чём не бывало! Но ведь искры летели реально! Ну и ладно, понаблюдаем как поведёт себя далее. Собрал, чуть подправив шкив напильником, там несколько ручьёв, надёжность не снизится.
Подключил через диммер, для снижения оборотов до минимума. Просто боялся перегреть металл при шлифовке режущих лезвий. Работает! Хоть у меня есть и вторая ленточная шлифовалка, но удобно пока одна остывает, пользоваться второй. У них очень сильно греются кольца из наждачной бумаги, абразив ведь, царапает, ну и выделяется тепло. Воздушное охлаждение с отсосом пыли и воздуха, уносящего тепло недостаточно. Даже с пылесосом, поэтому надо делать перерывы давая ленте охладиться. Во-первых, многие ленты просто расклеиваются от температуры. На горячую поверхность прилипает пыль и коксуется, пригорает, а это значит лента прослужит недолго.
На одну шлифовальную машинку я наклеил лист пробки. Материал из пробкового дуба, он великолепный теплоизолятор. Но тут столкнулся с парадоксом. Пробка хоть и износоустойчива и теплоизолятор, но с ней лента греется меньше, чем на второй машинке, у которой простая сталь в качестве подложки по которой прокручивается шлифовальная лента.
Я пока не понял в чём дело. Раньше я использовал пробку в качестве тормозных колодок на велосипеде. Штатные колодки скрипели, а пробковые и тормозили лучше в любую погоду и при торможении только шорох издавали. По идее лента должна была больше греться, но это не так. Возможно, кто-то просветит этот вопрос? Я предполагаю, что там где есть железная пластина, она сама греется и излучает в инфракрасном диапазоне нагревая ленту, так как площадь этой железки большая, а с пробковой подложкой, нагрев идёт только со стороны зёрен, но они и охлаждаются эффективнее при движении об воздух нежели тыльная сторона ленты которую ещё и железяка подогревает.
Вот. Ножи я сделал. Но до главного с чего начал так и не добрался. Петли из нержавейки не сделал, инкрустацию тоже. Но уже что-то описание и фоток накидал с горкой, видимо окончание ремонта солонки будет в следующем посте.
Пост о предыдущих ножах
Ножи с ручкой из чёрной акации. Лезвия из полотна сабельной пилы
Материалы для изготовления.
Проволока 8 мм диаметром.
Куски веток сантиметров 5-8 диаметром.
Листовая пружинная сталь.
Инструменты для изготовления.
Сварочный аппарат, токарный станок, шлифовальная ленточная машинка, сверлильный станок, молотки, свёрла, тиски слесарные, циркулярка, ленточная пила, напильники.
Расходные материалы.
Наждачная бумага от 40 грит до 600.
Масло льняное с пчелиным воском.
Фотографии процесса изготовления.
Как всегда, навалены горы инструментов и запчастей, каждый новый проект начинается с разбора рабочего места.
На этот раз задумал реанимировать солонку. Да, у меня такая солонка )) С 2004 года она честно служит мне.
Дело в том, что при высокой влажности дырочки в солонках забиваются, а тут забиваться нечему.
Она поприличней выглядела, я её просто забыл убрать с дождя. Но это дуб, ничего ему не будет. Морёный будет ))
Петли буду менять, сделаю нержавеющие.
Просто попутный разбору кадр. Плашка шелковицы светлая, но со временем темнеет, будет как держатель для свёрл и метчиков, те что на заднем плане.
Разборка рабочей поверхности закончена, сейчас начнётся заполнением инструментов и материалов для ремонта солонки.
Нержавейка потолще для осей петель и гвоздей, которыми буду петли крепить.
На столе уже наковаленка калёная, молотки, отвёртки.
Нержавейка очень крепкая, режу ножницами по металлу с трудом.
1,48 мм толщина.
Отрезал и отковал, держу в ручных тисочках, иначе по пальцам отбивает каждый удар.
Самый простой способ, иначе где брать нержавейку катанку, проще отрезать от листа и проковать.
Надо ведь немного.
Разборка до винтика ))
Шлифовка. Обратите внимание, силиконовым кругляком чищу ленту наждачной бумаги, тут для контраста почистил только одну сторону.
Лента очень быстро нагревается, периодически снимаю для охлаждения.
Гравёром выбираю морёный дуб ))
Вот такой фрезой слишком жёстко, аж щепки летят.
Внутри опилки от фрезы, а слева видно пыль древесную, это то что с солонки сошлифовал.
Сделаю помягче шлифовалку для внутренностей солонки.
Тут видно липучку для наждачки, но я её сниму, она была для тонкой наждачки, а сейчас будет 40 грит.
Производительность устраивает.
Закрепил в сверлильный станок самодельный шлифовальный торцевой барабан.
Сделан по-простому, наждачку надрезал сегментами и на клее обернул вокруг пробки от шампанского. Сегменты последовательно загнуты по ходу вращения.
Процесс шлифовки весьма быстр.
Ну и хватит пока, займусь крышкой.
Нарисовал рыбку, буду делать инкрустацию латунью.
Но это дуб. Мои ножи для инкрустации не лезут в контрольную дубовую плашку. Слишком велико усилие, надо более узкие ножи.
За время пока отковал, пока нарисовал, пока сделал барабан шлифовальный и т.д. На столе опять нет места ))
Ну ладно, вторая разборка от инструментов чтобы сделать новые ножи для инкрустации пригодные для работы с дубом.
Разобрал, пару веточек акации нашёл.
Ещё пару веток. Опилил их и нарисовал форму рукоятей.
На ленточной пиле вырезал по линиям.
Ну и опять, пошло-поехало, инструменты опять выкладываются на стол.
На этот раз пруток использую 8 мм. Ножи будут узкими, а крепости катанки хватит для удержания лезвия.
Делать буду по отработанной технологии, в паз вставлять клинок и приваривать электросваркой.
В паз в прутке, пропиленный болгаркой, вставляю стальную пластину и отпиливаю в размер.
Толщина пропила как раз по толщине стальной вставки.
Прошлый раз делал из полотна сабельной пилы, теперь из пружины листовой. Их применяли в старых стиральных машинах.
Будет несколько видов жал.
Косячок, прямой и попробую полукруглый сделать.
Согнуть пружинную сталь, надо постараться.
Я ведь без термички хочу обойтись, буду пробовать гнуть.
Сталь крепкая, разметку едва прочертил.
Слегка увлёкся ковкой и не делал фоток. Тут уже немного шлифованные и заточенные ножи.
Рукоятки просверлил. Известный способ, в токарный патрон сверло, и держа рукоятку ножа чтоб было удобно сверлю. Автоматически получается правильный хват рукоятки.
Глубина посадки хвостовика в рукоятку 100 мм. Во избежание раскола рукоятки при больших усилиях резания дерева. Пруток 8 мм толщиной, согнуть его руками при такой длине трудно, соответственно и деревянная рукоятка будет работать без особой нагрузки.
Сварка с медным теплоотводом.
Детальки мелкие, чуть пережал, и лопнуло. А может и ранее лопнуло при отковке на желобок. В любом случае если трещина будет мешать, то отломаю одну сторону и получится узенький нож, который мне тоже нужен ))
Аварийное завершение работ. С огненными брызгами.
Дома подходящих щёток не нашлось, пришлось ехать в магазин.
Рабочее место многократно в процессе работ то заполняется всяческим, то приходится разбирать чтобы добавлять новое.
Дополнительный регулятор оборотов к шлифовальной машинке. Пока без корпуса, собрал на дощечке для проверки. Работой доволен. Можно выставить самые малые обороты чтобы не перегреть металл при шлифовке. Корпус сделаю потом обязательно или встрою стационарно в блок розеток. Болгарку тоже можно запустить на самых малых оборотах, как и любой инструмент с коллекторным мотором.
Выточил деревянные переходники для установки алмазной чашки в сверлильный станок. У меня там коллекторный двигатель и регулятор оборотов с поддержанием мощности на валу.
В процессе работ очень быстро загромождается рабочая поверхность.
Для полировального диска тоже делаю переходники для установки в токарный станок.
Выпилил пару шайб, но маловат размер.
Разметил побольше диаметром.
Проточил по месту, что исключает биения диска.
На токарном нет электронной регулировки, обороты устанавливаются перестановкой ремня в разные ручьи шкивов..
Результат полировки вполне приемлемый.
Рукоятки обдираю грубо рашпилевой насадкой, потом наждачной бумагой 40 грит выравниваю поверхность.
Набор рукояток из чёрной акации.
Шлифовка 600 грит.
Новые ножи готовы.
Ножи готовы, масло льняное с пчелиным воском в качестве защиты от грязи и влаги.
Ссылка на видео:
Весь процесс изготовления с фотографиями и видео.
На рутубе
На ютубе есть несколько десятков видео с моими поделками. Если кому интересно, могу описать что и как делал.
Второй комплект ножей для инкрустации. Рукоятки из чёрной акации, лезвия из пружинной стали от старой стиральной машины. Лезвия сделаны меньшего размера чем у предыдущего комплекта, для работы с дубом, эвкалиптом и грабом. Они легче режут дерево поперёк волокон в силу своей узкой рабочей кромки. Конечно и с мягкими породами дерева можно работать ))
Становитесь автором сайта, публикуйте собственные статьи, описания самоделок с оплатой за текст. Подробнее здесь.