Приветствую Самодельщиков!
После мучений, скажем так, решил сделать обвес для сварочного аппарата. Мучения заключались в том что, работая на высоте не всегда было удобно электроды брать рукой в ахапку и пытаться засунуть в карман или поясную сумку они постоянно высыпались гнулись и т.д., а молоточек постоянно терялся даже если работать в мастерской. И также в мастерской приходилось искать пачки электродов, то упали куда-нибудь, то положил сверху материал и т.д.
В голову пришла идея прикрепить всё на корпус сварочника...
Пока на улице работа была не возможна из-за погодных условий, а сидеть не мог на месте без дела, взялся за самоделку.
[media=https://youtu.be/TbQKfOYu4PQ]
Инструменты и материалы:
- УШМ (болгарка)
- отрезные круги по металлу
- канализационные трубы Ф40мм (2 шт.)
- заглушки для канализационных труб Ф50мм (2 шт.)
- заглушки для канализационных труб Ф110мм (4 шт.)
- вытяжные заклёпки 3,2х10; 3,2х6; 4х10
- заклёпочник
- свёрла по металлу 3,5 мм; 4 мм; 16мм
- шуруповёрт или дрель
- кусок перегородочного гипсокартонного профиля 50х50
- бельевой шнур
- паяльник
- паяльная станция
- рулетка или линейка
- карандаш, маркер, шило (использовал для прочерчивания контура, так удобней было)
- оцинкованные шайбы 4 мм
- молоток
- тиски или наковальня
Шаг 1: Материал и размещение на корпусе.
Прежде чем браться и делать задуманное необходимо учесть габариты корпуса аппарата, размеры нужно знать для следующего:
- габариты должны быть компактными
- размещение должно быть на одной стороне
- в процессе работы пользование обвесом не должно создавать дискомфорта
Для тубуса под электроды самое оптимальное - труба, канализационная 40 мм вполне годится для этого. У неё есть плюсы: пластик достаточно прочный, дешёвый и самое главное лёгкий.
Имея в хозяйстве обрезки трубы 50 мм достаточной длины (всего лишь для выяснения расположения), для того чтобы понять как будет располагаться сам тубус, использовал их для определения места на корпусе. Замерять рулеткой габариты посчитал лишним, т.к. определять по факту удобнее когда уже знаешь из чего будешь делать.
Пока осваивал работу со сваркой, убедился в том что разрезанные пополам электроды удобнее чем в целом виде. Теперь постоянно режу их на две части по 17,5 см и на отрезанных частях сбиваю молотком порошок (не помню как правильно называется). Тубус длинной 35 см для целого электрода не возможно было компактно разместить на жестяном кожухе так чтобы и остальные идеи также разместились рядом.
Шаг 2: Тубус для электродов.
Разложив изначально в 50-ую и 40-ую трубы электроды, понял что 40-я труба вместительней, т.е. сделать из двух 40-х труб тубус по размерам лучше подходил чем из одной 50-ой. Но трубки нужны были с раструбом для соединения (далее объясню для чего), а поскольку у меня были обрезки без раструбов то пришлось поехать и купить. Ещё пришлось купить две заглушки для 50-ой трубы, из них я сделаю крышку чтобы электроды не высыпались если сварка наклонится.
По длине купил трубки 25 см, мне попадались 15 см, но в продаже их почему-то не было. Отрезать буду не 17,5 см от края, а чуть меньше 17,5, из того расчёта что крышка тоже имеет глубину почти 2 см. Приложил будущие крышки на раструбы трубы 40 мм и образуют крышку.
Отрезал меньше чтобы после среза лишнего у трубы, электроды выпирали за края в конце работы над тубусом. Лучше браться сразу за электрод чем пытаться выискивать его пальцами внутри.
Длина 17,5 см, а отмерил 18 см (0,5 см запас) от ребра на самой заглушке, от него и делал метку на самих трубках.
Торцевал трубы по метке с помощью листа бумаги. Обернул вокруг трубы, соединил края бумаги и склеил эти края клейкой лентой, отрезал с помощью ушм, на ней стоит регулятор оборотов и мне не пришлось пластик резать канцелярским ножом.
Как сторцевал трубки, решил вернуть фаски, они потребуются чтобы в дальнейшем можно было припаять дно.
Пластик для дна тубуса вырезал из тех же заглушек только уже для 110-ой трубы.
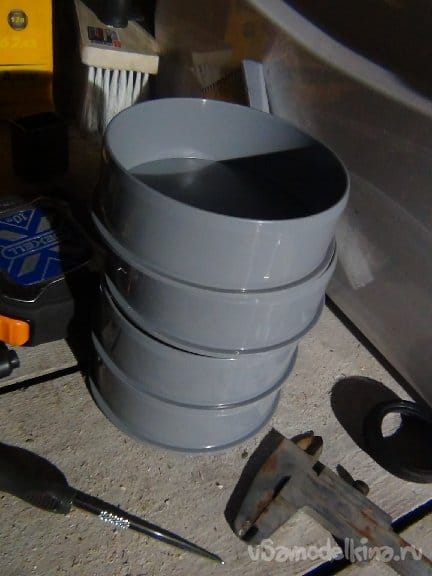
У меня где-то были куски такого же пластика, но было лень их искать, вот и решил приобрести данные заглушки. Чтобы получить из них плоский пластик для донца, с этих крышек срезал кольцо.
Оставшиеся кольца ещё потребуются, использую их как прутки для пайки, заранее разрезав их на ширину 3-4 мм ножницами по металлу.
Не желая тратить время на разметку маркером, установил отрезанные трубки на пластик и шилом процарапал окружности контуров. Далее вырезал ножницами по металлу. В итоге два дна, остаётся их припаять.
При использовании паяльной станции, т.е. паять прутком, сделал точечные прихватки обычным паяльником по дну и трубке, эти точки удержат дно на месте и не позволят сдвинутся крыглякам при пайке пластиковым прутком.
Получилось очень даже ничего, грубые края сгладил обычным паяльником. Почти товарный вид.
Почти всё, но остаётся за малым - крышка
Выступы на заглушках не позволят одеваться на трубки как запланировано. Придётся их обрезать по одной стороне и также срезать фаску. Данная работа облегчит их спайку в дальнейшем.
Решение срезать так обуславливается тем что, уж лучше срезать рёбра и трубки разместить поближе друг к другу чем оставить всё как есть и ловить миллиметраж между трубками. Но габариты тубуса ограничены размерами стенки жестяного кожуха сварки.
Между собой их спаял кусками которые остались после вырезки донцев. Обрезки не годятся уже, а для подобной работы как раз.
Чтобы крышка не разломалась в месте пайки, где были рёбра, решил также пропаять и по бокам. Чем крепче будет крышка тем дольше прослужит, да и дальнейшая задумка требует чтобы было именно так пропаяно иначе сломается.
Изготовление данных труб делается формовкой, если не ошибаюсь с названием процесса.
Расширения труб, в них изнутри находятся резиновые уплотнители, имеют не ровную форму. Её придётся шлифануть, иначе изготовленная крышка не будет надеваться на раструб и придётся что-то одно переделывать.
После данной работы приступаем к слиянию двух труб в один тубус.
Перед тем как спаивать трубки воедино, необходимо надеть на них крышку и зафиксировать скотчем, это не позволит трубкам сдвинуться относительно друг друга в процессе спайки.
Во время работы с пластиком остаётся много обрезков, но чтобы не выкидывать, по факту материал, пускаем его в дело, эти же обрезки нарезал кусками и вложил их на соприкасание раструбов, и поскольку в этом месте не было смысла паять станцией (всего 1-1,5 см) пропаял паяльником. На дне поступил также.
Над петлёй крышки пришлось подумать, были факты того что она не должна открываться в одну сторону, иначе было бы не удобно ей пользоваться (далее будет понятно почему). На пружинку, кусок тряпки или на вертлюг крепить её было бы не эстетично, поэтому решил использовать кусок полипропиленового шнура. На этом шнурке крышка может открываться и отодвигаться в любую сторону, данная идея оказалась кстати, крышку можно будет открыть и заправить за ёмкость с остатками электродов, я назвал эту ёмкость "пепельницей" (самое логическое название), и она будет располагаться как раз под тубусом.
Пока не снял ленту разметил места сверления для заклёпок 3,2х6 мм.
Лохматые концы шнура после обрезания ножом обработал паяльником. Затем чтобы установить заклёпку проткнул шилом и продёрнул. Перед установкой клёпки в пластик лучше подложить шайбу с обратной стороны, это стоит делать, т.к. заклёпки вытяжные и при установке может разорвать пластмассу.
Крышка не будет крышкой если она будет болтаться.
Надо было придумать замок, но простой, без ключа. Для удобства лучше сделать чтобы открыть можно было одним пальцем.
Сделал простой замок-защёлку из пластинки.
Пластинку вырезал около 6 см, такую длину сделал специально чтобы оставалось место для поддевания пальцем на открытие и прислонил её к ребру (см. фото).
Чтобы она не отломалась при первых же испытаниях, пропаял её как по ребру так и по бокам, после такой спайки она начала функционировать как пружинка.
Вместо петли, это же не замок, сделал небольшой выступ похожий на акулий плавник. Чтобы его сделать нужно просверлить через пластинку в трубу, задать направление. Если этот "плавник" припаять к поверхности то он отломается, а если его вставить в отверстие и оплавить изнутри то будет лучше держаться, я так и сделал.
Пластинку для "плавника"отрезал длиной в 1 см.
Всё таки пропаял и с внешней стороны.
Теперь "плавнику" придаём его форму, отпаял паяльником и сгладил оплавленный край. Скос сделал в сторону крышки, теперь всё работает как защёлка. Но по бокам от этого носика пришлось доработать напильником, чтобы пластинка надевалась без проблем.
Шаг 3: Крепление тубуса.
Перед сверлением необходимо снять кожух, чтобы стружка не попала на схемы и контакты.
В крайнем случае можно открутить стенку и подложить под неё или картон, или плотную бумагу, как это сделал я.
В голове перебрал множество креплений, но решил остановиться над тем что опишу далее.
Крепление требовалось не сильно крупным чтобы не мешало если тубус снят, т.к. не всегда работаю на высоте и надобности постоянно держать тубус на корпусе аппарата нет.
В итоге дальнейшее решение оказалось в тему, т.е. самым подходящим.
Принцип крепления как задвижка или засов.
Все элементы дальше вырезал из 110-х заглушек.
Крепление придумано как карман. Для этого необходимо вырезать две одинаковые детали для одного крепления, в одной из них будет вырезаться четверть куда будет вставляться планка-засов. Та в которой будет вырезаться часть будет прилегать к корпусу. Таких деталей потребуется 4 штуки.
Чтобы планка-засов без проблем входила в фиксатор, то меж деталями надо сделать зазор в 1 мм. При отпиливании кольца со 110-й заглушки остались выступы, они-то и пригодились.
Соединил две части крепления и просто спаял по грани обычным паяльником. В итоге имеем крепление для нижней части тубуса. Все части сделал аналогичным образом (фото далее).
Обрезанный край получается под углом 90 градусов, он будет упираться в сами крепления, где такой же срез. Чтобы этого избежать, болгаркой срезал фаску (угол произвольный).
В итоге такое решение облегчит снятие и обратную установку тубуса.
Засов сделал из пластинок из 110-й заглушки. Эти планки-засовы будут припаиваться к трубкам тубуса. За счёт таких замков тубус будет держаться крепко на кожухе сварки.
Фаски срезал болгаркой также как на самих креплениях, в процессе работы тестировал данный замок и убедился что фаски должны быть как на креплении так и на засовах.
Как все фаски сделаны, нужно припаять планки к трубкам и можно приступать к сверлению отверстий под заклёпки на сам корпус.
Но не всё так просто! Перед сверлением надо убедится что установленные заклёпки не будут мешать установке кожуха обратно на место на основной корпус где находятся внутренности аппарата. Кожух крепиться обычными шурупами на металлический каркас. Упустив этот не маловажный момент придётся пересверливать отверстия.
Отмерил от монтажных отверстий 5 мм в центр плоскости и отвёл карандашом линию ограничивающую край для заклёпок.
Как всё размечено можно доделывать планки-засовы.
Предварительно положив на корпус крепления и планки с тубусом начал двигать из стороны в сторону все детали дабы определится с местоположением. Как только определился с положением на трубках отметил места куда будут припаиваться планки. Тубус получается под наклоном относительно низа всей сварки.
Припаял засовы паяльной станцией по раструбу и внизу около дна прутком и обрезками от тех обрезков заглушки.
Перед сверлением, когда уже место определено точно, не отмечая маркером сделал проще, сильно прижал рукой к корпусу и просверлил шуруповёртом и крепления и кожух. Установил заклёпки 4х10 мм, по толщине и по длине самое оптимальное.
После завершения данной работы протестировал методом поднимания только за тубус, ничего не треснуло, всё держится крепко. Можно не бояться что если что-то может отвалиться в процессе работы.
Шаг 4: Ёмкость для остатков электродов.
Ёмкость для остатков электродов решил сделать из-за маленьких ошмётков какие остаются.
Работал на высоте, варил бантины в металлическом временном сарае, и остатки бросал под ноги. Спускаясь со стремянки за очередной порцией электродов наступил на такой ошмёток, он проткнул подошву моих рабочих берцев и чуть повредил мне ногу, не сильно, но ощущение было не приятным.
Назвал данную ёмкость "пепельницей", т.к. остаются такие же маленькие "окурки" от электродов что и от папиросы, по смыслу лучше названия не придумаешь.
В хозяйстве имеется множество обрезков от гипсокартонных профилей, сдаю в металлолом, и как раз на виду лежал кусок от перегородочного профиля 50 мм на 50 мм. Из него и решил сделать.
Размеры вышли 7х5х5 см, где 7 см это высота.
Сам кусок был длинной около 50 см, а мне требовался всего 17 см.
Коробочка получалась самая простая. Отрезал лишнее и загнул по прорезям в коробок, прям как в оригами.
Как крепить на сварочнике, собственно, ответ уже знаете! Так же как для тубуса. Мне нужно чтобы и эти крепления были так же не приметны если пепельница снята за ненадобностью.
Части профиля выгнул молотком на наковальне в одну плоскость с задней спинкой коробка, образовались два уха, как у тубуса планки-засовы.
Сам короб смонтировал на заклёпки 3,2 на 6 мм.
Как выше написал, данный коробочек будет находиться под тубусом, но шуруп корпуса мешал установке креплений, поэтому пришлось уши подрезать так, чтобы они упирались в сам шуруп, остатки электродов не 10 кг весят, так что и такие уши будут нормально, как говориться.
Здесь решил нижнюю часть сделать не пластиком, а двумя шайбами под одну клёпку.
Сверлил также как и для тубуса, сильно прижав рукой. Установил крепления на заклёпки 3,2х10 мм.
Шаг 5: Крепление для отбивочного молотка.
Как писал в начале, молоток (он конечно появился позже) и всякие предметы которые использовал для отбивки шлака постоянно терялись и забывались места где они потерялись...
Решил также сделать крепление для молотка, раз уж сделал его, и показал себя в деле вполне функционирующим.
Делать подобное крепление как в предыдущем описании не имела смысла. Вот тут я начал ломать голову как и куда его определить...
Много идей пронеслось как ветер в моей голове и решил сделать необычное крепление.
В дело пошло не задействованное кольцо от большой заглушки.
На первом фото вы уже могли увидеть это исполнение крепления.
Далее описание.
Покрутив в руках обод и молоток определился на таком виде (см. фото).
Поскольку молоток будет входить не прямой относительно центра, а как-бы по смещённой касательной, надо просверлить овальные отверстия.
После определения по высоте дуги относительно площадки будущего крепления, сделал метки где буду сверлить сначала сверлом по металлу 4 мм, а уже потом сверлом 16 мм, диаметр рукояти молотка сделал из 16 прута.
Чтобы получить овальное отверстие надо сначала просверлить перпендикулярно относительно окружности, путаюсь как правильно описать, а потом поворачивать в сторону другого отверстия, в итоге длина сверла позволила сделать сквозное отверстие, по направлению входа молотка и плоскости пластинки получаем овальное отверстие (см.фото). В последствии такое крепление показало себя с лучшей стороны и не пришлось придумывать дополнительный фиксатор молотка чтобы он не выпадал.
Монтажную пластинку для последнего крепления вырезал из остатков заглушки, по ширине как раз подходила и по длине тоже.
Остаётся дугу припаять к пластику, тут почти израсходовал не нужные остатки пластика. Паяльной станцией не было смысла, сделал это обычным паяльником.
Место определил для данного крепления на сварке сверху, сделал смещение вперёд, чтобы ремень находясь на плече в натянутом положении не мешал доставать молоток.
Приклепал на заклёпки 3,2 на 10 мм.
Процесс сверления также как и в предыдущих случаях, сильно прижал и просверлил.
Из этого же молотка, тут уже смекалка, получился не плохой крюк для переноски шлема (см.фото).
Когда направляешься к месту работы руки свободны для материала или ещё чего-нибудь...
Если будут вопросы то обращайтесь, отвечу :)
Становитесь автором сайта, публикуйте собственные статьи, описания самоделок с оплатой за текст. Подробнее здесь.