Как контролировать форму и кривизну детали? Если это плоскость, то вопрос с кривизной решается с помощью пробного стекла. Прополировав слегка поверхность детали, можно по виду полос определить её кривизну и принять меры к исправлению кривизны. Если нет пробного стекла, то приходится действовать головой. К детали следует пришлифовать самым мелким абразивом (например, пятимикронным) два небольших одинаковых стекла). Если их прополировать и сложить вместе, то разность их кривизны будет по абсолютной величине равна двойной кривизне детали на диаметре этих стёкол. Если их сделать равного размера с деталью, то точность измерения повысится и мы будем иметь известный «метод трёх стёкол». Он позволяет, в принципе, делать плоскости оптического качества, примерно до одной десятой полосы. Стёкла складываются попарно друг с другом. Разность их кривизны в полосах, которая при этом обнаруживается позволяет составить систему из трёх простейших линейных уравнений типа А+В=3, В+С=1, А+С=2. Решив её, можно узнать кривизну всех трёх стёкол.
Часто не требуется иметь точно плоскую поверхность. Например, достаточна сферическая поверхность очень большого радиуса кривизны — «квази-плоскость». Тогда можно сделать шлифовальник из стекла того же размера, что и деталь, прополировать его поверхность и сложив с деталью не по центру, обнаружить зонные ошибки. Окончательное уничтожение слабых и плавных «зон» можно отложить до окончания всей оптической системы, выявляя ошибки при теневом контроле. Окна ламп можно вообще не контролировать на кривизну, ограничиваясь использованием более-менее плоского шлифовальника.
Контроль клиновидности (разнотолщинности) плоскопараллельных пластин ведётся инструментом соответствующей точности. Для уничтожения в достаточной степени клиновидности окон ламп при обработке их второй стороны, достаточно переложить заготовки беспорядочным образом на наклеечном приспособлении. Образовавшийся на первом этапе «клин» при такой перекладке (разумеется, при достаточном количестве деталей) должен взаимно уничтожиться. Можно просто развернуть детали блока на 180 градусов, если их немного. При этом надо следить, чтобы тыльная сторона детали плотно прилегала к наклеечному приспособлению. При таком способе обработки следует применять «жёсткую» блокировку, при которой детали приклеиваются возможно более тонким слоем смолы или воска с канифолью. Из-за деформации деталей наклеечным приспособлением их форма неизбежно будет иметь астигматические ошибки. Во многих случаях это вполне допустимо. Точную поверхность на жёсткой блокировке изготовить нельзя. Астигматизма можно до некоторой степени избежать, наклеивая деталь мягкой и чистой полировочной смолой (не воском!) через ровную и хорошую резину толщиной примерно в миллиметр. Подходит медицинский резиновый жгут в виде широкой ленты. Следует особо остерегаться царапающих примесей между полированной стороной детали и металлом. При притирке детали они могут вызвать глубокие царапины.
Если требуются пластины более высокой точности, например, «окна» для йодной ячейки, то их контроль на всех стадиях шлифовки ведётся с помощью штангенциркуля и микрометра. Иногда можно допустить некоторые отступления от заданной толщины пластины. В таком случае её толщину можно контролировать штангенциркулем, а разнотолщинность по краю — самодельной скобой с микронным часовым индикатором.
Достаточно убрать «клин» до полмикрона и даже до одного микрона, чтобы на стадии полировки уничтожить его более основательно. Контроль при этом можно осуществлять с помощью простейшего интерферометра, направляя на пластину луч лазера с достаточно большого расстояния или расширив его двумя линзами до нужного диаметра. «Зайчик» от пластины следует навести строго по оси пучка на белый экран. Интерференционная картина покажет разнотолщинность, разность кривизны и разность ошибок поверхностей. Следует заметить, что такой простенький интерферометр может внести ошибку кривизны, если пучок света, падающий на деталь, не параллельный.
К этой же задаче (измерение разнотолщинности плоскопараллельных пластин) вплотную примыкает другая: центровка линз различного вида. В крупном производстве она, чаще всего, решается прошлифовкой обода линзы на центровочном станке после полной обработки её оптических поверхностей. В единичном и мелкосерийном производстве такая технология неприемлема по двум причинам: она требует большей заготовки, часть которой бесполезно стачивается и требует отдельного точного и дорогого станка. Кроме того, деталь большого размера может просто не поместится на центровочном станке.
Гораздо проще и дешевле применить следующий приём: в достаточно толстой плоской пластине из любого металла на резьбе крепится два штифта из железа. Расстояние между ними должно быть примерно 0,6 диаметра линзы. Заготовка линзы укладывается на пластину, упирается в эти штифты и обводится чертилкой. В полученном круге сверлятся три сквозных отверстия под резьбу М6 и, после нарезки, в них вворачиваются до упора низкие стальные штифты с скругленными головками. Люфтов быть не должно! Вместо них можно вбить в отверстия подходящие стальные шарики. Если теперь шлифованную заготовку линзы уложить на эти штифты и прижать к боковым штифтам, то при её вращении можно индикаторной головкой мерить разнотолщинность по краю. Заготовка не должна качаться на этих упорах, а боковые штифты должны упираться в цилиндрическую поверхность заготовки примерно на половине её высоты. Если кривизна линзы велика, то заготовка должна быть круглой с высокой точностью. Для плоских поверхностей это не обязательно. Если же заготовка имеет не круглую форму и это мешает измерениям, то её следует разметить на секторы и записывать результат измерения. Он должен совпадать для её симметричных сторон.
Если нижняя поверхность линзы должна быть вогнутой, то с этой стороны нашлифовывают неширокую плоскую фаску, которая, наряду с цилиндрическим ободом линзы, является базовой для обеих поверхностей. При плоской базовой фаске и одной вогнутой стороне можно не делать нижних штифтов, а укладывать линзу на достаточно плоское приспособление и вращать прямо на нём. Клин нижней поверхности измеряют, устанавливая индикатор в отверстие, просверленное в самой пластине. Он меряет снизу вверх.
Метод этот прост, удобен и универсален. Так можно убирать «клин» менисков диаметром до 300-400 миллиметров, наносить юстировочные поверхности на гиперболические зеркала кассегреновских телескопов, убирать клиновидность плоскопараллельных пластин. Для линз малого размера можно выточить временную оправку, привинтить её к приспособлению одним винтом и вращать линзу в ней. Такое приспособление позволяет легко уничтожить клиновидность с точностью до нескольких микрон. Необходимо только позаботится о его жёсткости и возможности надёжного крепления индикатора в нужной позиции.
Выявленный «клин» проще всего убирать на неподвижном шлифовальнике, сильнее нажимая на более толстую сторону детали. У неопытного мастера при такой работе может появиться «крыша» поверхности из-за того, что он слишком усердствует и чрезмерно стачивает стекло с одного края. Для её устранения достаточно прошлифовать всю поверхность обычным способом.
При таком способе центровки линз используется их симметрия относительно оптической оси. Призмы тоже обладают свойствами симметрии, используя которые, можно убирать «пирамидальность», разность углов и другие неправильности формы. В качестве измерителя при изготовлении призм можно применять накладное плоскопараллельное зеркальце с автоколлиматором или лазером, луч которого, при достаточном удалении экрана может служить хорошим указателем. Высокая когерентность излучения лазера позволит собрать простенький интерферометр для контроля прямого угла прямоугольной призмы с одновременным контролем однородности её стекла, контроля разности её двух других углов и пирамидальности с точностью долей полосы. Так же можно контролировать и уголковые отражатели («триппель-призмы»). Используя свойства симметрии, можно простыми способами контролировать и другие призмы.
Здесь мы должны подчеркнуть, что высочайшая точность изготовления оптических деталей, при должном прилежании и понимании мастером сути дела, может быть достигнута при весьма скромной производственной базе, хотя процесс изготовления детали будет, разумеется, более длительным, чем на специализированном оборудовании. В лабораторных условиях это вполне допустимо, так как позволяет экономить время, например, на поиске подрядчика и получить деталь такого качества, которое требуется. Если нужное качество не получится, то опять же винить никого, кроме самого себя, не приходится, а такая обида быстро забывается. Точность самих поверхностей при финишных операциях может быть проверена различными методами, но их можно свести к наиболее употребительным: теневой метод, интерференционный и «метод конечного результата».
Наиболее универсален и прост теневой метод. Его суть вот в чём: Проверяемая поверхность устанавливается в такую оптическую схему, в которой есть хотя бы две анаберационные точки. (Они могут быть совмещены.) Например, это фокусы удлинённого эллипсоида, центр кривизны сферической поверхности, ближайший фокус параболоида и «бесконечность» и т. д. Часто (например, у вогнутой сферы) такая система может состоять только из самой этой поверхности, в других случаях её приходится дополнять (например, параболу — плоскостью или сферическим вогнутым зеркалом). В одной из анаберационных точек устанавливается (или строится с помощью вспомогательной оптической системы, если эта точка — мнимая) близкий к точечному источник света. Тогда свет, пройдя систему, построит в другой точке изображение этого источника, которое будет также безаберационным, если все поверхности имеют нужную форму и система сьюстирована. Перекрывая конус лучей в точке схождения непрозрачным экраном — «ножом Фуко» и поместив глаз таким образом, чтобы оставшийся свет попадал в него весь, можно увидеть «теневую картину» в виде грубых «неровностей рельефа».
«Нож» должен быть тем острее и ровнее, а юстировка системы тем более точной, чем больший угол схождения лучей, чем светосильнее исследуемый пучок. Для систем со светосилой в точке контроля меньше одной десятой можно вместо точечного источника применять даже нить накаливания маленькой лампочки, если она достаточно компактна. Лучше, конечно, применять меньшую «точку». Если она не связана с «ножом» (например, находится в другом фокусе эллипсоида) то её можно осуществить, засвечивая по оси системы маленький блестящий шарик при помощи автомобильной лампочки с простейшим однолинзовым конденсором. Меняя диаметр конденсора с помощью диафрагмы из чёрной бумаги, можно менять размер «точки» которой служит блик на шарике.
Разумеется, при правильной фокусировке лампочки этот блик является сильно уменьшенным изображением конденсора, а не нити накала. Устанавливая на конденсор диафрагмы различного вида можно получать «точки» произвольной формы и размера (например, в виде «двойной звезды»). Размер их составляет размер конденсора делённый на расстояние «конденсор-шарик» и умноженный на четверть диаметра шарика. Шарик можно применять от шарикоподшипника. Он не должен иметь царапин и грязи на поверхности. Для больших «точек» он вполне подходит, но точки дифракционного размера с ним получить трудно. Особенно мешает грязь на поверхности шарика. Для их осуществления следует брать шарик, специально изготовленный из чёрного стекла и тщательно отполированный. Протирая его чистой тканью, можно получить чёткий блик, размер которого (повторяем!) будет равен диаметру конденсора, делённому на расстояние от него до шарика и умноженного на четверть его радиуса. Для очень светосильных систем шарик следует брать меньшего размера из-за вносимых им аберраций.
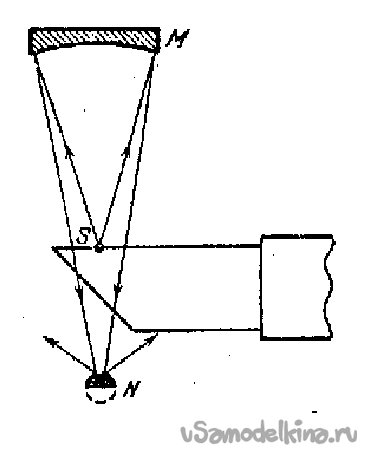
Рис. 4. Дополнительный узел к теневому прибору т.н. осветитель высокой апертуры, где: S – световое окно теневого прибора; небольшое вогнутое зеркало М; N – шарик.
Пока ошибки поверхности велики, блик следует брать большим, по мере уменьшения ошибок следует переходить к стеклянному шарику и малому диаметру конденсора. Из-за потерь света иногда приходится ставить в осветитель шаровую ртутную или ксеноновую лампу высокого давления, либо устанавливать на конденсор щелевидную диафрагму. Впрочем, как показал Максутов, увеличения «точки», если её край резкий, не приводит к сильному увеличению ошибок контроля. В пределе чувствительность теневого метода раз в сто превышает требуемую для получения первоклассной поверхности. Однако он не даёт количественной меры ошибок, поэтому его часто дополняют «окулярной пробой». Очень малую «точку» (её изображение) рассматривают в сильный окуляр с фокусным расстоянием в 1-10 мм.. Перемещая окуляр вдоль оптической оси, наблюдаем внефокальные изображения «точки». Если например, предфокальное изображение имеет вид «баранки», а зафокальное — диффузное, то мы имеем общую ошибку поверхности «сплюснутый сфероид», или, что то же самое — «вогнутый тор». Если же картина противоположная, то поднята средняя зона поверхности («выпуклый тор», «гипербола»).
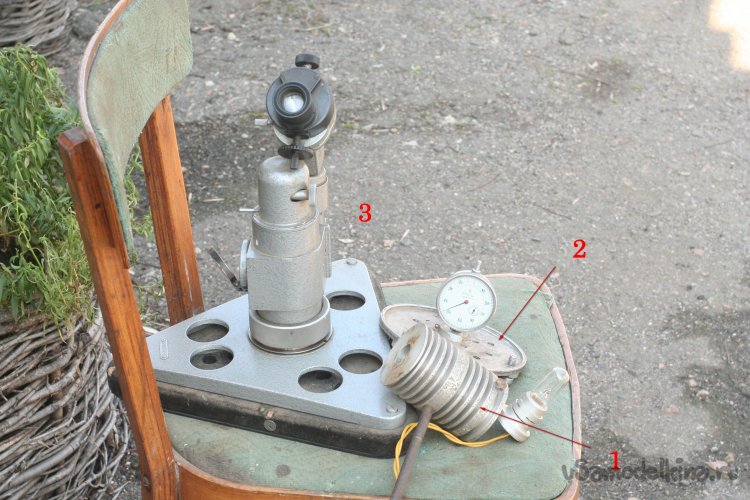
Фото 5. Где: 1 – осветитель для засветки шариков; 2 – самодельный контактный сферометр; 3 – накладной сферометр ИЗС-8 для контроля кривизны больших и тяжелых деталей.
Фото 6.
Фото 7.
Рис. 8. Устройство осветителя шариков, где: 1 – шарик на подставке; 2 – объектив осветителя; 3 – лампочка; 4 – патрон лампочки в оправке; 5 – корпус осветителя; 6 – стопорный винт.
Фото 9. Сферометр ИЗС-7 для небольших линз, из лаборатории автора.
Следует заметить, что теневой метод требует некоторой тренировки и «понятия». Автор знал одного очень неглупого человека, который освоить этот метод так и не смог! «Прямую» картину видно при контроле отражающих поверхностей. Преломляющие поверхности показывают «бугор» на месте «ямы», что следует учитывать, например, при ретуши менисков или пластинок Шмидта.
Фото 10. Фабричный теневой прибор ТП-1 для исследования и контроля поверхности астрономической оптики, из лаборатории автора.
Рис. 11. Оптическая схема теневого прибора, где: 1-автомобильная лампа; 2,3-объективы; 4-зеркало; 5-зеркальная металлическая площадка; 6-вращающийся диск.
Для систем, фокусы которых можно совместить (например, сферическое зеркало) применяется «теневой прибор» в котором нож и «точечный» источник света связаны между собой и перемещаются вместе. (См.рис.выше) Такой прибор изготовить не представляет особого труда, и если оптика делается регулярно, он становится незаменимым рабочим инструментом. Его осветитель, однако, следует выполнить иначе, в виде алюминиевого радиатора, а лампочку поместить внутрь вытяжной трубы. Тогда прибор меньше греется и можно применить мощную лампочку, например, галогенную 12вольт и сто ватт. Лампа должна иметь компактное тело накала, иначе её мощность не даёт ничего кроме излишнего нагрева.
Фото 12, 13. Самодельный теневой прибор автора с автомобильной лампой.
Поставив вместо лампочки полупроводниковый лазер, такой прибор можно превратить в интерферометр, конструкцию и принцип действия которого мы предоставляем читателям разработать самостоятельно. Он позволит измерять ошибки волнового фронта количественно.
Применяя двукратное отражения света от контролируемой поверхности, можно удвоить чувствительность метода. На линзах она составляет около четверти чувствительности для отражающей поверхности (при однократном прохождении света). Этот же метод можно применить ко всей телескопической системе, установив её против хорошей плоскости и работая из фокуса телескопа.
Этот метод можно отнести к «проверке по конечному результату». Если система работает не так, как следует, то изготовитель, которому неплохо быть и пользователем одновременно, исправляет одну из поверхностей, компенсируя этим ошибки всей системы. Поскольку этим методом мы убираем именно сферическую аберрацию, то надо ретушировать поверхность, стоящую в зрачке системы. Например: в системе Шмидта ретуши подлежит именно пластинка, а не зеркало, которое должно быть сферическим.
Метод «по конечному результату» состоит в том, что исследуется вся система целиком, и ей, как целому «вправляются мозги» до тех пор, пока она не будет работать так, как нужно. Непременное условие для этого — наличие собственных мозгов у того, кто вправляет, иначе нечего будет вправлять. Метод применим и к неоптическим системам, особенно — с большим количеством независимых параметров.
Интерференционный метод контроля имеет множество модификаций (в том числе — сложных и дорогих) и применений (в том числе, и для контроля оптики на заводах.) При изготовлении оптики в лабораторных условиях он чаще всего применяется к небольшим плоскостям. Этот метод требует плоского «пробного стекла» достаточной точности, которое может применять к любым деталям. Иногда интерференционный контроль применяют к выпуклым деталям, используя вместо «пробы» слегка прополированную и проверенную теневым методом стеклянную контрдеталь, шлифовальник. Это позволяет измерить местные ошибки поверхности, а общие определяются теневым методом.
Стекло накладывают на деталь (или наоборот) и освещают монохроматическим светом ртутной или неоновой лампы. Можно применять и натрий. Удобно использовать бактерицидную лампу ДБ-30, но её необходимо закрыть оконным стеклом для защиты от сильного ультрафиолета или одеть на неё вымытую сорокамиллиметровую трубку от лампы дневного света. Не следует относится к ультрафиолету небрежно. Глаза он поражает не сразу, но основательно, может и кожу обжечь!
Фото 14, 15, 16. Светильник автора для интерференционного способа контроля, на основе самодельных ртутных ламп тлеющего разряда.
Фото 17. Интерференционная картина, светильник сверху.
Если для контроля применять белый свет, то детали и пробу следует тщательно чистить, чтобы зазор между ними не превышал одного микрона.
Освещение может быть двух видов: освещают большой белый экран, например — потолок. Кольца наблюдают, по возможности, с того же направления, с которого падает свет. Тогда контроль будет наиболее точен. Можно также взять маленький источник света, например, любую неоновую лампочку и превратить расходящийся пучок света в параллельный с помощью плоско-гиперболической линзы. Тогда удобно выполнить её плоскую сторону в виде точной плоскости и использовать её для контроля. При этом можно использовать близкий к точечному источник света малой мощности (например — неоновую лампочку). На базе такой линзы можно сделать простой и удобный интерферометр для контроля призм (см. Рис 18).
Рис. 18. Интерферометр для контроля поверхности призм, с плоско-гиперболической линзой, где: 1 - плоско-гиперболическая линза; 2 – призма; 3 – зеркало; 4 – шарик; 5 – наблюдатель.
Преимущества такого интерферометра в том, что освещение производится по нормали к плоской поверхности и не мешает вторая сторона детали. К тому же, лёгкая деталь, накладывается на массивную пробу, что не приводит к сильным деформациям детали. Смотреть на интерференционные полосы можно сверху вниз, под некоторым углом. Недостаток — прямой контакт между стёклами, что может привести к царапинам.
Смола.
Полировка деталей высокой точности производится на полировальнике, изготовленном из специальной смолы. Для полировки деталей малой точности, вроде линз очков, может применятся сукно, наклеенное смолой на металл.
«Смолой» в данном случае называется гидрофобная некристаллическая и текучая композиция, основным компонентом которой обычно является канифоль. Для размягчения канифоли и увеличения гидрофобности в неё добавляют древесный или каменноугольный пек, касторовое или даже, подсолнечное масло, скипидар, воск и другие компоненты. Твёрдость смолы обычно подбирают «на зуб». Смола не должна крошится при разжёвывании. Зубы и ноготь должны оставлять на ней отпечатки. Точнее текучесть смолы корректируют по рабочей температуре. Чем холоднее в помещении, тем смола должна быть мягче. И наоборот. При работе смолой температура в помещении должна быть как можно стабильнее. Оптимальная температура — 22-25 град. Цельсия. (Сукно может полировать при любой разумной температуре.)
Именно полировка на смоле даёт возможность относительно простыми средствами получить ту высочайшую точность, которая необходима для оптических поверхностей. Причём, эта точность часто получается автоматически. Для получения, например, сферической поверхности надо просто полировать «правильно» — «хорошей» смолой с штрихом в одну треть диаметра, правильно изготовить полировальник, следить за его подрезкой и т. д. Однако практика показала, что далеко не всякая смола даёт поверхность приемлемого качества. Часто при теневом контроле поверхность выглядит «рваной», с большим количеством мелких зонок, при этом, обязательно — имеет «завал» края. Наоборот, иногда поверхность «идёт» сама, теневая картина «гладкая» и на ней видны лишь большие и плавные неоднородности поверхностей.
Переход от одного вида к другому может происходить при изменении температуры (её повышение приводит к выправлению «рваной» поверхности). При замене полирита крокусом поверхность детали также становится глаже. Получению гладкой поверхности способствует замедление хода станка и уменьшение штриха. Последняя мера, однако, может привести к появлению зонок.
Отмечен случай, когда при полировке в сепараторе полировальник отлично работал два дня, после чего перестал приполировываться к большому стеклу и начал делать завалы на деталях. «Рваная» поверхность выглядит так, будто полировальник работает не всей своей поверхностью, а отдельными участками и те участки детали, которые начали по какой-либо случайной причине полироваться быстрее других, приобретают повышенную мягкость, способность сполировываться ещё сильнее.
Первоначально мы считали, что лучше всего, почти идеально должна работать та смола, которая не имеет упругости и течёт при любой малой нагрузке. Такую смолу можно получить, сплавляя канифоль с касторкой. (См. книгу Агеннера). Она имеет также то преимущество, что не содержит канцерогенных компонентов, например тех, что есть в каменноугольном пеке. Однако такая смола работает не лучше и не хуже других. Показала свою непригодность для точных работ канифоль с добавкой большого количества нефтебитума. Это более-менее понятно — нефтебитум проявляет заметную упругость и наверняка плохо прилегает к стеклу. Идеально работала смола, полученная из жидкого каменноугольного пека и канифоли. Она была битком набита ароматикой, воняла нафталином, но давала хорошие поверхности. Древесный дёготь, полученный из абрикосовых косточек, а также из берёзового дерева выдающихся результатов не дал. Слабым утешением служит то, что плохую полировку и «рваную» поверхность автор видел и на крупной оптике (1м. сфера из ситалла), изготовленной другими мастерами.
В отечественных книгах о полировке стекла (например, в монографии Винокурова) этот вопрос также не освещён. Те критерии, которые там приводятся (вязкость и прочность, скорость полировки) к получению поверхностей очень высокого качества прямого отношения, скорее всего, не имеют. Скорость полировки для нас не очень важна. Лучше за два часа отполировать поверхность, которая почти не нуждается в ретуши, чем за час такую, которую затем придётся «доводить» много дней.
В настоящее время можно констатировать, что есть более-менее вероятные предположения насчёт «плохой» смолы: Это: 1) Какие-то вредные явления на границе смола — полирующий порошок или на границе стекло — полирующая суспензия. 2) Смола представляет собой сложную, не познанную до конца тиксотропную систему, которая, с учётом разнообразия рецептов, ведёт себя так, как её заблагорассудится. 3) Кинематика станка подобрана плохо.
Последнее предположение наименее вероятно. Автор работал со смолой, на которой было почти невозможно «сорвать край» и на такой, где и односторонний штрих не давал нужного результата. 4) Может быть и такой эффект: При шлифовке стекла металлическим шлифовальником в нём вскрываются поры, а в них проникает вода. Потом, когда на этот металл клеим смолу, она закрывает поры, а в них начинается реакция воды с алюминием и выделяется водород. Он вспучивает смолу и искажает её поверхность во время работы. Тогда этот эффект не должен проявляться, если основание полировальника стеклянное или, перед наклейкой смолы прогрето при температуре намного выше ста градусов и пропитано воском.
Можно привести следующие рекомендации: Работать при стабильной температуре. Методом «научного тыка» найти «хороший» рецепт, состоящий из доступных, имеющих постоянные свойства компонентов, либо создать их запас на много лет вперёд и работать, используя этот рецепт. Достать запас «хорошей» смолы и работать с ней всегда. «Втереться в доверие» к «знающему человеку», и выведать у него секреты мастерства (если он их сам знает). Разобраться самому в механизме формообразования особо точных поверхностей и сознательно изготовить нужную смолу, которую затем и правильно использовать.
Последний путь, не пройденный автором, может быть и не самый перспективный, зато самый интересный и его мы можем порекомендовать. Начать следует с того что наделать много-много различных смол, полировать ними стандартные детали (например, сферы диаметром миллиметров 150 с фокусом в метр и писать в лабораторный журнал результаты и сопутствующие факторы. Может быть, удастся найти ключевой момент в этой каше.
Для успешной работы посредственной смолой можно рекомендовать не слишком низкую температуру помещения (по одному из наших наблюдений, переход от «плохой» работы к «хорошей» происходит при повышении температуры выше 22-х градусов). Способствует получению гладких поверхностей крокус с низкой температурой обжига (700-750 градусов) вместо полирита и других быстроработающих порошков, мягкая смола.
Разумеется, для не слишком точных деталей (одна четвёртая полосы) пригодна и не слишком хорошая смола.
Здесь мы упомянём ещё несколько моментов: Для полировки гидрофильного стекла употребляется гидрофобная смола и гидрофобный полирующий порошок в воде. Для полировки металлов с оптической точностью следует поступить наоборот: применять гидрофильную смолу и гидрофильный порошок, а воду заменить неполярной жидкостью. Это предположение вполне согласуется с результатами Винокурова (См. лит.)
Очень гладкая зеркальная поверхность (которая, однако, оптически не контролировалась) была нами получена, когда мы взяли в качестве смолы специально сваренный композит из сахара и глицерина, своеобразный «леденец», а в качестве порошка — мелкую окись алюминия (М-3) и керосин вместо воды. Мы прополировали случайную алюминиевую деталь (поверхность старого шлифовальника) из сплава АЛ-2. Полировка шла быстро. Однако, полировальник пришёл в негодность из-за поглощения влаги воздуха и перестал работать. Таким полировальником можно работать только в «сухой» камере. Однако, если взять вместо «леденца» гидрофильную целлюлозу, например — полотно, то этот процесс, аналогичный полировке стекла сукном можно производить в обычной атмосфере. Разумеется, точность поверхности при этом снизится.
В этой же главе мы кратко рассмотрим полировку суконным полировальником. Наверное, самым лучшим материалом для этой цели может служить тонкое шинельное сукно. Другие виды шерстяной ткани также пригодны, но они должны быть прочными, с не очень длинным ворсом и небольшой толщины. Гладкость и малая толщина способствуют получению более точных поверхностей. Суконная полировка раньше широко применялась для полировки зеркального стекла, поэтому её теория хорошо разработана и подробно описана (например, Качаловым)
Сукно нужно как следует вытряхнуть от пыли и наклеить на металлический инструмент не очень толстым слоем смолы. Её не надо слишком перегревать до текучего состояния, чтобы она не сильно впитывалась в сукно. Слой смолы должен быть равномерным. Ещё горячий полировальник следует отформовать деталью и, охладив струёй воды (беречь от неё разогретое стекло!) начать полировку. Для наклеивания сукна можно применять и другие водостойкие клеи, например — 88-И. Полирующие порошки можно применять те же самые, что и для работы на смоле, однако, поскольку точные поверхности при полировке на сукне всё равно не получаются, то преимущество следует отдать быстро работающим порошкам. Суконный полировальник тоже можно подрезать, соскабливая поверхность сукна ножом на ходу станка.
Матовость снимается сукном не так, как смолой. Она как бы «слизывается» и после её устранения надо снять и образованные на месте выколок пологие ямки. Однако, в целом, сукно работает быстрее смолы, позволяет применять форсированные режимы работы, не прилипает к детали после высыхания полирующей суспензии, что позволяет оставлять станок на некоторое время без надзора. При работе на больших оборотах с высоким давлением и непрерывном охлаждении детали и инструмента струёй суспензии, отполировать небольшие детали можно за несколько минут. Качество суконной полировки вполне достаточное для очков и окон ламп.
Литература.
1. Д.Д. Максутов. Изготовление и исследование астрономической оптики. Москва, «Наука», 1984 г.
2. Д.Стронг. Техника физического эксперимента. Лениздат, 1948 г.
3. Некоторые особенности обработки стекла при изготовлении (астрономической) оптики в кустарных условиях. Часть 1. Общие положения.
4. Некоторые особенности обработки стекла при изготовлении (астрономической) оптики в кустарных условиях. Часть 2 . Заготовка, абразивы, растворители, инструменты.
Бондаренко Ю. Н., Маяки 2018 г.